製造業において、製品の品質と信頼性を確保するためには、寸法検査が欠かせません。寸法検査は、製品が設計図面通りの寸法や公差を満たしているかを確認するプロセスであり、不良品の流出を防ぎ、再作業や納期遅延のリスクを低減します。また、ISOやJISなどの国際規格に基づいた検査基準や、AIやデジタル技術を活用した最新の検査手法も登場しています。本記事では、寸法検査の基礎知識から最新動向までを詳しく解説し、製造現場での品質管理の向上に役立つ情報を提供します。
寸法検査とは
製造業には欠かせないキーテクノロジー
寸法検査は、加工部品が図面で指定された長さや角度、公差に収まっているかを判定し、製品が設計どおりに機能することを確実にする工程です。検査を通じて不適合品を工程内で隔離できれば、後工程への波及を防ぎ、再作業コストや納期遅延の発生率を大幅に抑制できます。さらに取得データを統計管理すれば、設備ごとの加工ばらつきを定量化し、工程能力指数を上げるための根拠を得られます。品質保証とプロセス改善の双方を支える、製造業には欠かせないキーテクノロジーだといえます。
寸法公差と設計図面の読み解きポイント
図面に示される公差は、安全性や組立互換性を確保するための境界値です。検査担当者は幾何公差記号や基準面への指示を読み解き、どの面を基準に寸法を測定すべきか判断する必要があります。JIS B 0021やISO 1101などの規格を理解していれば、設計意図を正確に汲み取り、誤った測定基準を適用するリスクを大幅に減らせます。とりわけ複雑形状では、投影図と補助断面図の照合を怠ると測定点を誤認する恐れがあるため、事前に図面を3D化し、仮想的に測定箇所を割り出す作業が推奨されます。
寸法測定が生産効率に与える影響
測定データをリアルタイムでNC工作機にフィードバックすれば、工具摩耗や熱変形による寸法ずれを加工中に補正でき、スクラップ率が飛躍的に低下します。検査時間が短くても精度が伴わなければ逆効果ですが、インラインで自動化した測定システムを使えばタクトタイムを維持しつつ全数判定が可能です。結果としてライン停止の原因となる再加工が激減し、OEE(総合設備効率)が改善します。加えて、検査履歴を工程FMEAに組み込めば、リスク優先度数を定量的に更新でき、メンテナンス計画を科学的に最適化できます。
ISO・JIS規格に基づく検査基準
自動車や医療機器など認証取得が必須の産業では、ISO 9001やIATF 16949に沿った品質マネジメントシステムを構築し、校正トレーサビリティや測定不確かさの算定を求められます。JIS B 7502など測定器ごとの国内規格も併用し、国家計量標準に直結した基準器で定期校正を行うことで、内部監査やサプライヤー監査に対応可能なエビデンスを示せます。こうした仕組みを整えると、拠点間で測定結果の再現性が一致し、グローバル生産にありがちな品質格差を最小化できます。
寸法検査プロセスによるコスト削減効果
不良流出は製品保証費用だけでなく、顧客信頼の失墜という無形コストを伴います。検査を強化し初期流動段階で問題を封じ込めれば、保証コスト削減とブランド価値維持を同時に達成可能です。さらに検査データをSPCで管理すると、工程能力指数Cpkの推移から予防保全の適切なタイミングを把握でき、計画外停止を減らしながら工具寿命を最大限活用できます。結果として生産コスト構造が底上げされ、利益率向上につながります。
主な寸法検査方法と測定機器
ノギス・マイクロメーターなど手動測定器の活用メリット
デジタルノギスは液晶表示により読み取りミスを防ぎつつ、ワンタッチゼロリセットで測定準備を迅速化できます。マイクロメーターはねじ機構による微細送りで、10 µm以下の高精度測定を容易にします。近年はBluetooth機能を搭載したモデルが普及し、測定値をタブレットへ自動転送して記録ミスを排除できます。低コストで導入できるため、多品種少量生産の現場でも柔軟に使い回せることが大きな利点です。
三次元測定機(CMM)による高精度測定
CMMは接触式プローブで得た座標点から形状を再構築し、輪郭誤差や円筒度など幾何公差の適合性を一括判定できます。リニアスケールと温度補正モデルを組み合わせれば、1 µm台の測定保証が可能で、航空機エンジンや精密金型の品質管理に重宝されています。自動プロービングパス生成ソフトを使えば、プログラム作成工数を大幅に短縮できる点も魅力です。
レーザースキャナー/光学センサーの非接触測定技術
ラインレーザープロファイラは、高速振動するライン上でもワーク表面の3Dデータを瞬時に取得でき、金属プレス品のバリ高さや曲げ角度をリアルタイムで監視します。白色干渉計はナノオーダーの段差も読み取れるため、半導体露光マスクや医療用カテーテルなど繊細な製品でも形状変化を非破壊で確認できます。非接触ゆえキズのリスクがゼロで、再検査も容易です。
画像処理×AIのインライン寸法検査システム
高解像度カメラ群と深層学習モデルを組み込んだシステムでは、輝度ムラや個体差をネットワークが自動補正し、多数の測定点を一度に算出します。測定結果はエッジコンピューティングで即時判定され、不適合品はシュートで自動分別されるため、ライン停止なしの全数検査が実現します。収集データはクラウド統合され、複数工場の品質傾向をダッシュボードで可視化できます。
測定機校正とトレーサビリティ確保のポイント
測定器の精度は経年で変動するため、ISO 17025認定機関での周期校正が不可欠です。校正証明書には不確かさと参照標準が明記され、検査値の妥当性を第三者に説明できます。さらに校正管理ソフトを導入すれば、期日が迫った機器を自動でアラートし、校正漏れを根絶できます。これにより内部監査・外部監査をスムーズに乗り切れます。
寸法検査の課題と改善策
検査リードタイム短縮と自動化支援ツール
ロボットハンドがワークを保持し、そのままCMMへ搬入して測定まで自動で行うセル生産システムが登場しています。AIは測定点の優先度を学習し、短時間で主要寸法を抽出するため、サイクルタイムを維持しつつ不具合流出ゼロを狙えます。タブレットで工程進捗を可視化すれば、段取り替えのタイミングも現場全員で共有でき、停滞が解消されます。
オペレーター依存による測定ばらつきの抑制策
ばらつき要因を排除するため、作業姿勢を固定化する治具や、測定面に磁性ガイドを設けて接触角度を一定に保つ工夫が有効です。また動画マニュアルとARグラスを活用し、測定位置をリアルタイムで重ね表示すれば、新人でもベテランと同じ精度を再現できます。教育コストを抑えながら品質を統一できる点が大きなメリットです。
温度・振動など測定環境が寸法誤差に与える影響
寸法測定は環境温度20 ℃を基準に行うのが一般的ですが、工場内は四季で大きく変動します。恒温室を完備できない場合は、測定器に温度センサーを搭載し、測定値をリアルタイム補正するアルゴリズムを用いると効果的です。さらに防振台をCMM下に設置し、プレス機の衝撃を低減すれば、μmレベルのブレを抑えられます。
SPC(統計的工程管理)によるデータ分析活用法
測定結果をXbar-R管理図へプロットし、±3σ外の外れ値を検知すれば、工程が統計的管理状態から逸脱する前に対策できます。短タクト製品にはI-MR図を採用し、サンプルサイズが1でも異常を追跡可能です。得られたデータをヒストグラム化して分布特性を把握すれば、加工機のチューニング指標として活用できます。
良品学習AIでリアルタイム異常検知を実現
不良ラベルが十分に集まらない場合でも、オートエンコーダー型AIは良品のみを学習して異常スコアを算出します。異常スコアがしきい値を超えたワークを即座に排出できるため、突発的な刃具欠損や治具ずれにも迅速に対応可能です。推論はGPUエッジデバイス上で行われ、クラウドレス運用でも5 ms以下の応答が得られます。
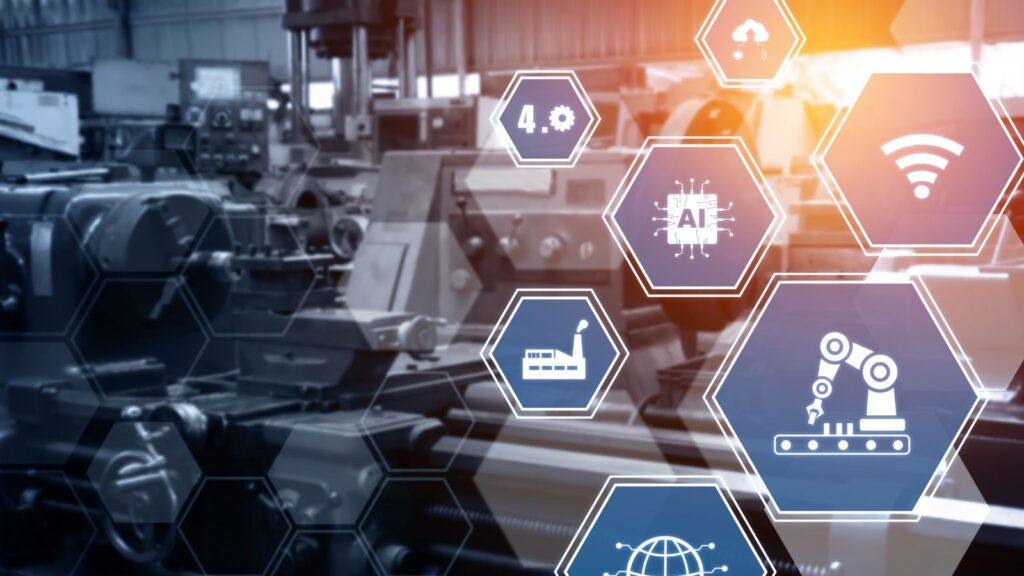
業界別活用事例を見ていきましょう
自動車部品:エンジン・ギアの公差管理事例
エンジンの心臓部であるクランクシャフトは、丸さや軸間の位置がほんの少しずれるだけで燃費や耐久性が落ちるため、量産工程でも非常に厳しい寸法管理が行われます。工場では人が測り切れない数のポイントを自動測定できるロボット付き三次元測定機を活用し、わずかな時間で詳細データを取得。測定結果はその場で加工機に送り返され、刃物が摩耗してずれが出始めた瞬間に条件が自動調整されます。この仕組みにより不良品の発生はごくわずかに抑えられ、蓄積したデータは次の改善サイクルにも役立つため、ライン全体の品質が年々底上げされています。
航空宇宙:複雑形状部品の非接触三次元測定
飛行機やロケットに使われる翼やタービンの部品は、複雑な曲面を持つうえに熱処理で変形しやすく、触れて測るとキズが付くおそれがあります。そこで工場ではレーザー光で表面をなぞり、数百万点もの立体データを一気に取得する非接触方式を採用。コンピューター上で理想形状と重ね合わせると、わずかな歪みも色分け表示されるため、作業者は修正が必要な場所だけをピンポイントで手直しできます。このプロセスにより合格率はほぼ100%に近づき、得られた点群はデジタルツインにも流用され、最終組立の精度予測や保全計画にも活かされています。
半導体・電子部品:マイクロ寸法測定の最新動向
半導体チップやスマートフォン用部品は、人の髪の毛より細い配線幅が並ぶ超微細世界です。製造ラインでは光を干渉させて厚みや幅を測る専用装置が取り入れられ、できあがるたびにパターンをチェック。収集されたデータはAIが瞬時に解析し、露光光量や薬液の濃度がわずかにズレても自動で最適条件に微調整します。これにより歩留まりが数パーセント単位で向上し、検査に費やす時間も大幅に短縮。見えない領域の品質をAIが支えることで、最先端デバイスの安定供給が可能になっています。
医療機器:安全性を担保するクリーン検査フロー
体内に入る人工関節やカテーテルは、表面の滑らかさや寸法のわずかな違いが患者の安全に直結します。そのため塵ひとつ許されないクリーンルームに非接触型の測定機を設置し、製品を一つひとつ丁寧にチェック。測定結果はバーコードで個体番号とひも付けられ、もし後にリコールが必要になった場合でも、いつ・どこで・誰に使われた製品かをすぐに追跡できます。測定の誤差範囲まで証明書で管理している点が監査でも高く評価され、海外への輸出ビジネスを後押しする信頼基盤となっています。
樹脂成形:射出成形品の収縮変形対策
プラスチック製のギアやコネクタは、金型から外れた後に冷えて縮むため、歯形や差し込み穴が変形しやすいのが課題です。最近はロボットが成形直後に部品を三次元スキャナーへ運び、歯面の形をすぐにデジタル化。AIが過去のデータと照合して最終的な縮み方を予測し、金型の温度や冷却時間を次ロットから自動調整します。その結果、不良品は劇的に減り、検査の手間も半分以下。蓄積されたデータは金型改良のシミュレーションにも使われ、開発期間の短縮にもつながっています。
AI・デジタル技術が切り開く寸法検査の未来
AIディープラーニングで検査精度をアップグレード
深層学習モデルはサブピクセルレベルのエッジ抽出と特徴量解析により、従来見逃されていた微小寸法差を高確度で検出します。学習済みネットワークをエッジGPUに展開すれば、1フレーム50ミリ秒以下で推論が完了し、タクトタイムを妨げません。説明可能AI(XAI)が根拠領域をハイライト表示するため、現場オペレーターも判定理由を直感的に把握できます。モデルはオンライン学習で日々最適化され、不良モードの多様化にも追従できる点が大きな強みです。
5G/IoTでつながるリアルタイムモニタリング
5Gの超低遅延通信を活用し、測定値をクラウドへ秒単位でアップロードする仕組みが実装されています。本社品質部門はダッシュボード経由で国内外の工場データを同時閲覧でき、異常傾向を捉えた瞬間に遠隔指示を出せます。IoTゲートウェイは加工機の振動・温度ログも取得し、測定データと時系列で重ね合わせてAI解析を実施します。複合的な要因を短時間で切り分けられるため、原因究明のスピードが飛躍的に向上し、計画外停止を最小化できます。
デジタルツイン×寸法検査で予測保全を実現
CADモデルと実測データを連携したデジタルツイン上では、工具摩耗や熱変形が時間経過とともにどの程度寸法に影響を与えるかをリアルタイムで可視化できます。シミュレーション結果がしきい値を超える前にアラートが発報され、保全担当者は最適な交換タイミングを把握できます。これにより計画外停止を回避しながら工具寿命を最大限活用でき、メンテナンスコストと在庫コストの双方を最適化できます。生産計画との連携も進み、工場全体の稼働率が底上げされています。
自律移動ロボットによるインライン検査の可能性
AMR(自律搬送ロボット)に高解像度3Dカメラを搭載し、ライン間を自律走行させることで、夜間も無人で全数検査が継続できます。撮影した点群はオンボードGPUで縮約処理され、異常が検出された場合のみクラウドへ送信されるため、通信量が最小化されます。判定結果はラインのPLCに直接フィードバックされ、不適合品は自動で排出される仕組みです。人手不足対策と検査コスト削減を同時に実現しつつ、24時間体制で品質を維持できる新しいアプローチとして注目されています。
サステナビリティ視点のコスト最適化とCO₂削減
高精度検査は歩留まりを改善し、材料廃棄を大幅に抑制するため、製造工程のCO₂排出削減に直結します。さらにAIが最適切削条件を提示することで必要以上の加工を防止し、工作機の電力消費を削減します。検査データをLCA(ライフサイクルアセスメント)に組み込むことで、製品のカーボンフットプリントを数値で示せるようになり、ESG投資を重視する顧客への説得力が高まります。品質向上と環境負荷低減を同時に達成できる点が、次世代ものづくりの大きな強みです。
まとめ:寸法検査が競争を勝ち抜く決め手に
寸法検査は品質保証を支える基盤技術であり、データ解析やAI技術と組み合わせることで、単なる合否判定を超えて生産全体を最適化する時代へ入りました。各社は測定器の高度化だけでなく、校正管理やデータ活用体制まで含めた総合的な改革を進めることが、競争を勝ち抜く決め手となります。
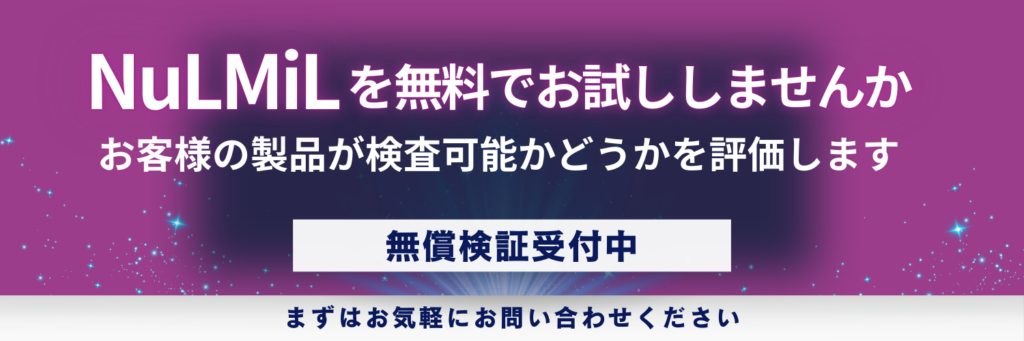