導入の背景
ある焼結金属加工企業では、製品の外観検査を1名の作業員による目視で行っていました。この検査では、凹み・たまり・ピット・異物などの欠陥を確認する必要がありましたが、次のような課題がありました。
- 手作業での検査には限界があり、見落としのリスクがある
- 他社メーカーによる外観検査でも同様の課題に直面し、解決策が見つかっていなかった
- 1名での検査は負担が大きく、安定した品質管理が難しい
- より効率的な検査手法を取り入れ、作業の省力化を図りたい
こうした状況を改善するため、当社の自動検査システムを導入いただくことになりました。
導入したソリューション
導入したのは、手動投入・手動排出を組み合わせた自動検査システムです。自動検査システムの導入に、手動投入と手動排出を組み合わせて作業の効率化を行いました。この仕組みにより、目視検査の負担を軽減しつつ、AIによる自動検査で品質の安定化を実現しました。
導入の成果
今回の導入により、作業員が大きな欠陥を作業員の目だけで確認する必要がなくなり、検査の精度が向上しました。また、手動投入・排出の工程を残すことで、現場に適した柔軟な運用が可能となり、スムーズな導入が実現しました。
導入にかかったコストは以下の通りです。
- 自動検査システム一式導入:2000万円~3000万円
- 人件費の削減と作業効率の向上により、長期的なコストメリットが生まれる
今後の展望
本システムの導入により、手作業と自動検査の最適な組み合わせが確立され、より安定した品質管理が可能になりました。今後は、検査のさらなる効率化を進めることで、より高度な生産体制の構築を目指します。
当社の自動検査システムは、製品の検査工程の効率化を実現し、高精度な品質管理をサポートします。手作業検査の限界を感じている企業様に、ぜひご検討いただきたいソリューションです。
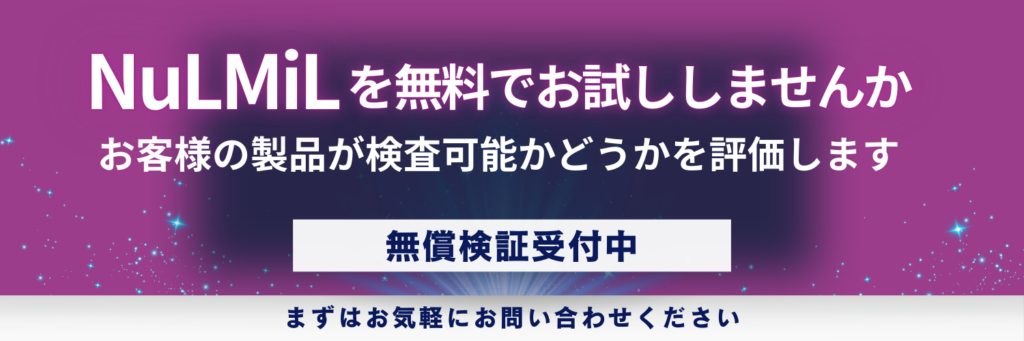