製造現場や生産管理において、「タクトタイム」「サイクルタイム」「リードタイム」といった用語はよく耳にします。これらは、生産効率の向上や工程の見える化に欠かせない指標ですが、初めて聞く方にとっては用語が混同しやすく、どのような違いや関係性があるのか分かりにくいかもしれません。
本記事では、初心者にも理解しやすいように、各指標の基本概念とその違い、さらには相互の関係性について詳しく解説していきます。
1. タクトタイムとは?
タクトタイムとは、生産ラインにおいて、顧客の需要に合わせた生産ペースを維持するために必要な時間のことです。具体的には、決められた期間内に必要な製品数を生産するために、各工程での作業間隔(時間)を算出する指標です。
例えば、1日の稼働時間が480分で、顧客からのオーダーが240個の場合、タクトタイムは「480分÷240個=2分」となります。つまり、2分ごとに1個の製品を完成させる必要があるという意味です。
タクトタイムは以下の特徴を持っています。
- 需要に直結: 顧客の注文数に応じて生産スピードを設定するため、無駄な在庫や過剰な稼働を防ぎます。
- 現場の見える化: タクトタイムを基に生産工程を管理することで、ボトルネック(生産の遅れが発生する工程)を特定しやすくなります。
- 改善の指標: 工程の遅延やムダを減らすための改善活動の目標設定に役立ちます。
2. サイクルタイムとの違い
サイクルタイムは、ある作業工程を一つ完了するまでにかかる時間を指します。タクトタイムとの大きな違いは、サイクルタイムはあくまで各作業の実際の処理時間や待ち時間、移動時間などを含めた実績値であるのに対し、タクトタイムは「目標」としての理論値である点です。
具体的には:
- タクトタイム: 「何分で1個作る必要があるか」という理論上の生産ペースを示す。
- サイクルタイム: 実際に1個の製品が出来上がるまでにかかった実績時間。
このため、サイクルタイムがタクトタイムより長い場合は、生産ラインに遅延が生じていることを意味し、短い場合は待ち時間や在庫が発生している可能性があります。
また、サイクルタイムは個々の作業者や工程ごとに異なり、改善活動の効果測定に利用されることが多いです。各工程のサイクルタイムを正確に把握することで、どこに改善の余地があるのかを特定し、効率的なラインバランス(工程間の負荷分散)を実現する手段ともなります。
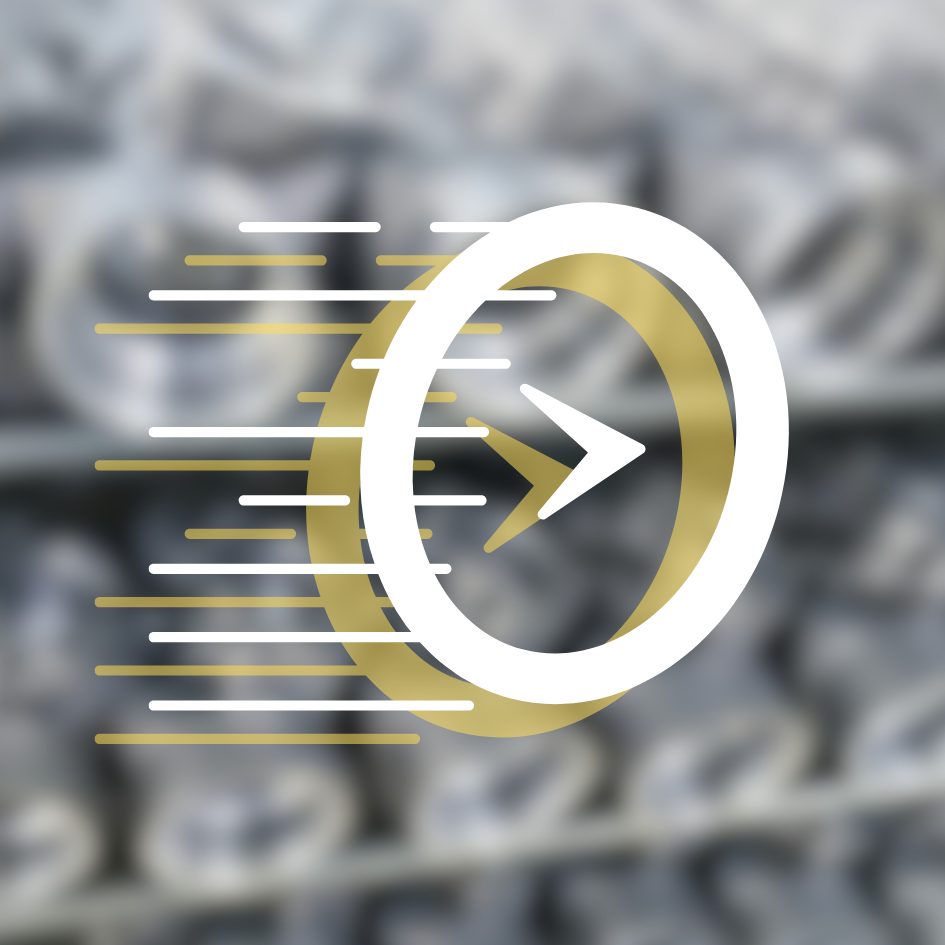
3. リードタイムとの関係性
リードタイムは、製品の注文を受けてから実際に納品されるまでにかかる全体の時間を示します。ここでのポイントは、リードタイムはタクトタイムやサイクルタイムと比較して、より広い視点での時間管理を目的としているという点です。
リードタイムは以下の要素を含みます:
- 加工時間(サイクルタイム): 製品が実際に作られる時間。
- 待ち時間: 部品や材料が次工程に渡るまでの待機時間。
- 移動時間: 工程間での移動や物流にかかる時間。
- 検査・調整時間: 製品品質を保証するための検査や修正にかかる時間。
このように、リードタイムは製造プロセス全体のパフォーマンスを測る指標となり、短縮が求められることが多いです。リードタイムの短縮は、顧客満足度の向上や在庫コストの削減に直結します。また、リードタイムの改善活動では、各工程でのサイクルタイムやタクトタイムのバランスを見直すことが重要となります。
4. それぞれの指標が持つ意味と現場での役割
タクトタイムの役割
タクトタイムは、顧客需要に合わせた生産計画の基準となります。製造ラインの各工程がこの基準を守ることで、全体の生産リズムが一定に保たれ、無駄な在庫の発生を防止します。生産現場においては、
- ラインバランスの見直し: 各作業の負荷が均一化され、特定工程に作業が偏るのを防止。
- 標準作業の策定: タクトタイムを基準に、各作業手順の標準化や教育を行う。
サイクルタイムの役割
サイクルタイムは、実際の生産効率を計測するための実績指標です。ここからは、現場での課題や改善の方向性を具体的に洗い出すことができます。
- ボトルネックの特定: どの工程が遅延の原因となっているかを把握。
- 作業改善の効果測定: 改善施策を実施した後、サイクルタイムの短縮が見られるかどうかをチェック。
リードタイムの役割
リードタイムは、顧客が実際に製品を受け取るまでの全体の流れを把握するための指標です。これにより、
- 顧客満足度の向上: 短いリードタイムは、迅速な納品を意味し、顧客の期待に応えることが可能。
- 在庫管理の効率化: 製品が市場に出回るまでの時間を最適化することで、在庫コストを削減。
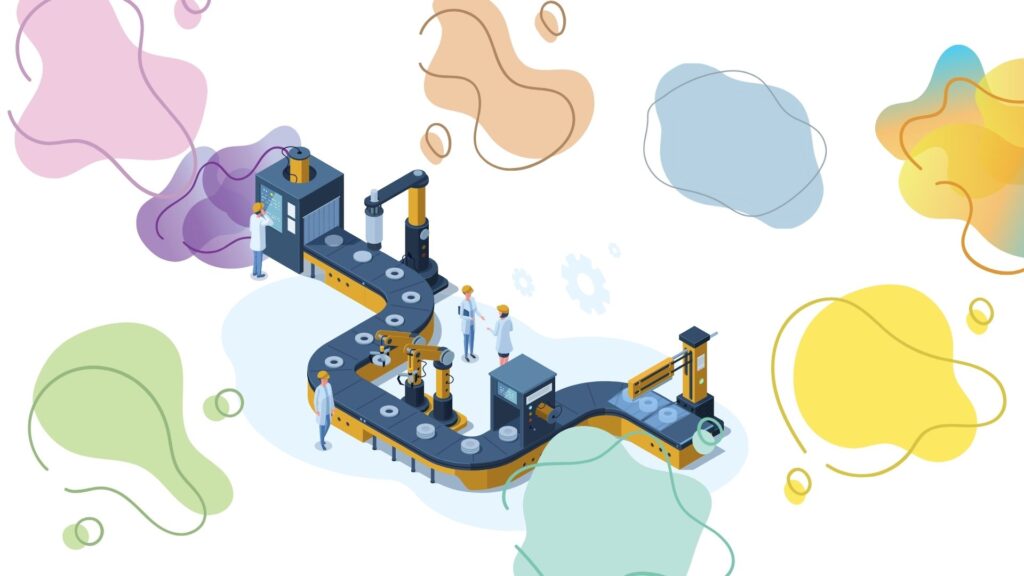
5. 各指標の相互関係と生産管理における改善ポイント
タクトタイム、サイクルタイム、リードタイムはそれぞれ独立した指標ですが、実際の生産現場では密接な関係性を持っています。
- 生産ペースの整合性: タクトタイムが設定されれば、各工程はこのペースを基準に稼働します。しかし、実際にはサイクルタイムがこの理論値より遅れることがあるため、その差異を如何に改善するかが鍵となります。
- 工程間のバランス: サイクルタイムが均一でない場合、どこかで作業が滞り、結果としてリードタイムが長くなります。そこで、工程ごとの作業負荷の均一化が求められます。
- 改善活動のフィードバックループ: タクトタイムを基準にしながらも、サイクルタイムの実績値を常にチェックし、必要に応じたプロセス改善を行うことが、全体のリードタイム短縮に繋がります。
ここで注目すべきは、単に各指標を個別に短縮するだけでなく、全体としてのバランスを考えることが重要であるという点です。例えば、ある工程でサイクルタイムを無理に短縮しようとすると、品質低下や作業者の負担増加といったリスクが伴います。現場では、タクトタイムを守るための現実的な改善策として、作業者の技能向上や自動化、設備の効率化など、総合的な視点で取り組む必要があります。
6. 初めての方へのアドバイスと実践事例
生産管理の指標としてタクトタイム、サイクルタイム、リードタイムを活用する際、初心者が押さえるべきポイントは以下の通りです。
- 基本概念の理解:
- まずはそれぞれの定義と役割をしっかり把握しましょう。タクトタイムは理論上の「目標」、サイクルタイムは現実の「実績」、リードタイムは「全体の流れ」として位置づけると分かりやすいです。
- 現場データの収集:
- 現状の生産工程の各タイムを正確に計測し、タクトタイムとの差異を明確にすることが大切です。改善前の現状把握は、改善策の効果を検証するための基礎となります。
- 段階的な改善活動:
- いきなり全体を大きく変えようとするのではなく、まずは一部の工程から改善を試み、その成果を他の工程にも展開するアプローチが効果的です。
- コミュニケーションの徹底:
- 作業者や管理者間で、現状の課題や改善策についての情報共有をしっかり行い、現場全体で改善活動に取り組む姿勢が求められます。
実際の企業事例として、ある製造業の現場では、タクトタイムを基準に作業の標準化を徹底することで、サイクルタイムのばらつきを減少させ、結果としてリードタイムの短縮に成功した例もあります。改善プロセスの中で、各工程の細かい動作や待ち時間を見直し、無駄な工程の削減と自動化の導入が奏功したのです。これにより、全体の生産性向上だけでなく、作業者の負担軽減にもつながったという報告があります。
まとめ
本記事では、タクトタイム、サイクルタイム、リードタイムという三つの重要な生産管理指標について、それぞれの定義と役割、そして相互の関係性を詳しく解説しました。
- タクトタイム: 顧客需要に合わせた理論上の生産ペースを示し、現場の目標となる指標。
- サイクルタイム: 実際に作業が完了するまでの時間を計測し、現場の実績を反映する指標。
- リードタイム: 注文から納品までの全体の流れを示し、顧客満足度や在庫管理に直結する指標。
これらの指標は、単独で評価するのではなく、全体のバランスや改善活動のフィードバックループとして捉えることが重要です。実践にあたっては、まず現状を正確に把握し、問題点を特定した上で、段階的に改善を進める姿勢が求められます。生産現場では、常に改善の余地があるため、定期的な見直しと情報共有が不可欠です。
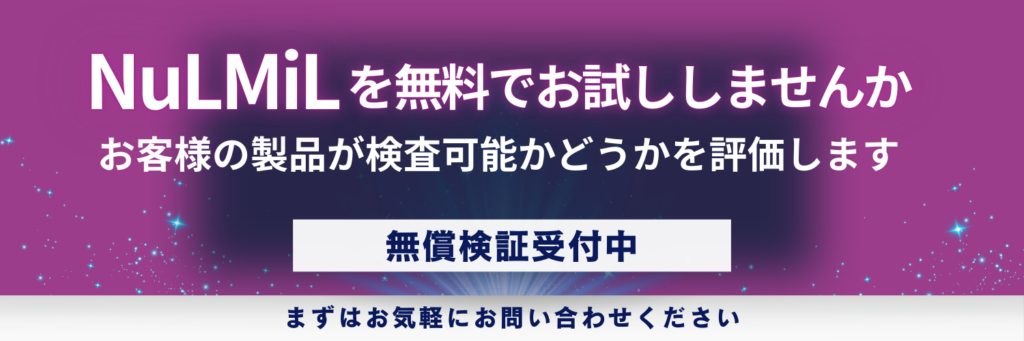