外観検査ではどんな項目を検査するのか?
外観検査は、製品の品質を保証し、顧客に信頼される製品を提供するために非常に重要なプロセスです。この検査では、製品の外観に関わる多くの項目がチェックされ、不良品が市場に出回るのを防ぎます。特に、製造業の効率化と品質向上において欠かせないステップであり、どの業界においても不可欠なものです。ここでは、外観検査で検査される主な項目を詳しく説明します。
1. 仕様・形状・寸法の検査
仕様や形状、寸法の検査は、製品が設計通りの形状やサイズで製造されているかを確認する重要な工程です。例えば、欠損や変形があると、機能面で問題が生じる可能性があり、特に自動車や航空機部品のような精密機器では致命的な欠陥となることがあります。寸法がわずかに異なるだけでも、部品が正しく組み合わさらず、不具合が発生することがあります。
この工程では、製品が規定の形状や寸法を保っているか、設計図や仕様書に基づいて厳密にチェックされます。また、意匠や印刷の検査も含まれ、ロゴや文字が正確に印刷されているか、意図した色調で製品が仕上がっているかが確認されます。デザインが正しく再現されていない場合、製品の印象やブランド価値が損なわれる可能性があります。
2. 製品表面の検査
表面検査では、製品の外観に傷や凹凸、異物の付着がないかを確認します。製品の見た目が重要な要素となる家電製品や日用品では、この検査は特に重要です。消費者はまず製品の外観に目が行くため、傷や汚れがあると、品質に対する印象が悪くなることがあります。
また、表面の感触や見栄えも重要なチェックポイントです。凹凸、シワ、ツヤ、ムラといった要素が消費者の満足度に直結するため、外観検査ではこれらの点を入念に確認します。たとえば、電子機器では、傷や埃の付着が性能や安全性に影響を与えることもあり、慎重にチェックする必要があります。
3. 色・仕上がりの検査
色や仕上がりの検査では、製品が設計通りの色調や質感を持っているかを確認します。色ムラや変色が発生している場合、製品の印象が大きく変わり、顧客にマイナスの印象を与えることがあります。これにより、ブランドの信頼性が損なわれることもあるため、色の一貫性を保つことが重要です。
また、仕上がりに関しては、バリや突起、加工跡が残っていないかも検査されます。特に消費者に直接触れる部分では、滑らかな表面であることが求められ、突起物があると怪我を引き起こす可能性があるため、不良品とされます。
4. 組み立て後の検査
製品の組み立てが正確であることを確認するために行われる組み立て後の検査は、特に重要なステップです。製品が正しく組み立てられていない場合、機能に重大な支障をきたすことがあります。具体的には、ネジや接合部がしっかりと固定されているか、バリや突起物が残っていないかが確認されます。
この検査は、安全性にも直結しており、不十分な組み立ては消費者の怪我や事故を引き起こすリスクを増加させます。そのため、外観検査の最終段階では、製品が正しく機能することを保証するための厳密なチェックが行われます。
5. 不良発生の原因調査
外観検査の最も重要な目的の一つは、不良発生の原因を調査し、改善策を講じることです。検査で発見された不良品は、その発生原因を特定するために、製造プロセスを遡って分析されます。この情報は製造工程にフィードバックされ、今後の製品の品質向上に役立てられます。これにより、再発防止策を講じることができ、最終的には生産効率の向上やコスト削減にもつながります。
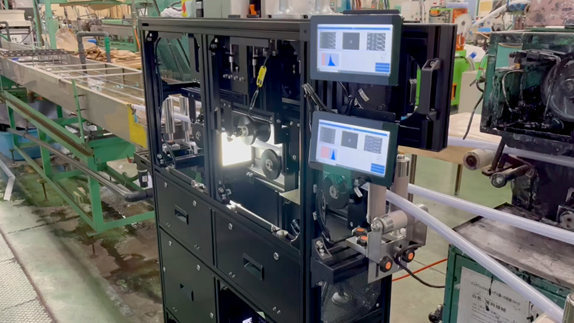

業界別の検査例
外観検査は、多様な業界で実施されており、各業界に応じた独自の検査項目が存在します。電子部品業界では、プリント基板の実装位置のズレや断線を確認することが重要です。金属部品業界では、表面の傷や変形が安全性に影響を与えるため、厳密な検査が必要です。食品業界では、包装の破損や異物混入を検出することが、消費者の安全確保に直結します。
外観検査は、製品の品質保証において不可欠なプロセスです。仕様・形状・寸法の確認から、製品表面の傷、色の均一性、組み立ての丁寧さに至るまで、多くの項目が検査されます。これにより、不良品の流出を防ぎ、製品の品質を維持することができます。適切な外観検査を実施することで、製品の信頼性が向上し、最終的にはブランド価値の向上にもつながります。
このように、外観検査は製品の品質と消費者の信頼を守るための重要な工程であり、あらゆる業界で欠かせない役割を果たしています。
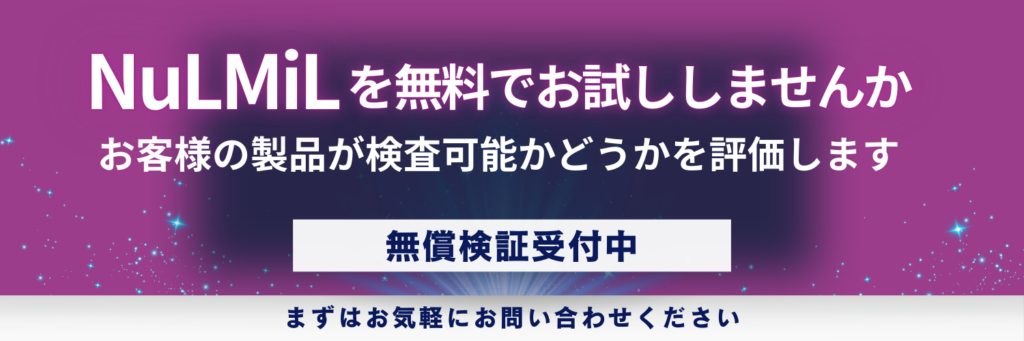