製造業をはじめとする多くの業界で、人手不足や品質要求の高度化といった課題が深刻化しています。このような状況を打開する鍵として、「検査業務の自動化」が今、大きな注目を集めています。従来の人の目に頼った検査から、AIやロボットを活用したシステムへと転換することは、単なる省人化に留まりません。この記事では、検査業務の自動化がなぜ必要なのかという基礎知識から、工数削減や生産性向上に直結する具体的な導入ポイント、さらには未来の生産現場像に至るまで解説します。
検査業務自動化の基礎知識と最新トレンド
なぜ今、検査業務の自動化が求められているのか
現代の日本の産業界は、少子高齢化に伴う労働人口の減少という、避けては通れない課題に直面しています。とりわけ、熟練した技術や高い集中力を要する検査業務は、担い手の確保と育成が年々難しくなっています。その一方で、消費者や取引先から求められる品質レベルはますます高くなるばかりで、人の目による見逃しは企業の信頼を揺るかねません。こうした背景から、個人の「経験」や「勘」に頼るやり方から抜け出し、安定的かつ高精度な品質を保つための仕組みとして、検査業務の自動化が重要な経営戦略となりつつあるのです。
自動化の導入がもたらす主なメリット
検査業務を自動化する仕組みは、企業に多くの良い変化をもたらします。第一に挙げられるのが「品質の安定と向上」です。機械は24時間365日、決められた同じ基準で検査を続けるため、担当者の熟練度やその日のコンディションによるバラつきがなくなります。次に期待できるのが「生産性の向上」です。スピーディーな自動検査は、生産ラインの流れをスムーズにし、全体の作業効率を高めます。さらに、これまで検査を担当していた人員を、より創造的で付加価値の高い仕事へ配置転換できるため、「省人化と人的資源の有効活用」にも繋がります。検査データをデジタル情報として蓄積・分析し、「製品の追跡管理(トレーサビリティ)」や「不良原因の早期発見」に役立てられる点も大きな利点です。
従来型検査との違いと課題
これまで主流だった人の目による検査(目視検査)は、人間の柔軟な判断力が強みです。予期せぬ不良や複雑な形状であっても、状況に応じて対応できる利点があります。しかし、その裏側には「判断基準の曖昧さ」という根深い課題が存在します。検査員それぞれで「これくらいならOK」「これはNG」といった判断に少しずつズレが生じ、品質を完全に一定に保つことが困難です。また、長時間の作業からくる疲れや集中力の低下が、見逃し(ヒューマンエラー)の危険性を高めてしまいます。こういった個人に依存する要素を取り除き、数値に基づいた客観的な基準で合否を判定できる点が、自動検査との根本的な違いです。
自動化に活用される主な技術(AI・ロボット・画像処理)
検査の自動化を支える中心的な技術は、主に3つ挙げられます。一つ目は「画像処理」技術です。これは、カメラで撮った製品の画像から、あらかじめ設定したルールに基づいて傷や汚れ、寸法の違いなどを見つけ出す技術です。二つ目は、近年めざましい発展を遂げている「AI(人工知能)」、特にディープラーニングと呼ばれる技術です。たくさんの良品・不良品の画像をAIに学ばせることで、まるで人間のように、曖昧な不良や初めて見る欠陥までも見分けられるようになります。三つ目は「ロボット」技術です。人の腕のように動くロボットが、製品を運んだり、向きを変えたり、検査後に仕分けたりといった物理的な作業を代行し、完全な無人化をサポートします。
業界別に進む自動化の事例紹介
検査の自動化は、すでに様々な業界で成果を上げています。自動車業界を例に取ると、AIを使った画像検査で、エンジン部品の目に見えないほどの細かな亀裂や、塗装のわずかなムラなどを正確に検出しています。電子部品業界に目を向ければ、非常に高精細なカメラと画像処理技術を組み合わせ、スマートフォンの基板にある髪の毛よりも細い配線の断線や、米粒より小さな部品のズレを瞬時に見つけ出しています。また、食品や医薬品の工場では、パッケージの印字ミスや異物の混入は絶対に許されません。ここではX線検査装置や画像認識システムが、私たちの食卓の安全・安心を守るために活躍しています。
工数削減に直結する自動化のポイント
作業標準化と省人化のコツ
検査業務の自動化を成功させるための土台として、「作業の標準化」が欠かせません。これは、誰が作業しても常に同じ結果を出せるように、明確な「仕事のルールブック」を作成するようなものです。検査する製品の置き方、照明の当て方、OKとNGを判断する基準といった全ての要素を具体的に定めることが第一歩となります。このルール作りの過程で、実は不要だった手順や、人によってやり方が違っていた作業などが明らかになります。それらを整理・統一するだけでも、作業の効率は上がり、工数を削減する効果が生まれます。自動化とは、この完成したルールブックを、機械に正確に実行させるプロセスなのです。
自動化システム導入で削減できる作業工程
自動化システムを導入すると、検査業務に含まれる多くの手作業をなくすことができます。一連の流れを想像してみてください。製品を一つずつ検査台に置き、角度を変えながら目で見て、結果を用紙に記入し、不良品を別の箱に入れる。こうした作業のほぼ全てが自動化の対象です。ロボットアームが製品をラインから取って検査装置にセットし、機械が製品を回転させながら複数のカメラで一瞬でチェック。判定結果は瞬時にデータとしてサーバーに保存され、不良品は自動でラインから弾かれます。この仕組みが、検査員を単純な繰り返し作業から解放し、検査そのものだけでなく、記録や仕分けといった付帯業務の時間も大きく減らします。
無駄な工程・重複作業を見える化する方法
自社の検査工程に隠れている無駄を発見するためには、仕事の流れを「見える化」するのが効果的です。具体的なやり方として、仕事全体の「フローチャート(工程図)」を作成してみましょう。製品がラインに運ばれてきてから、検査を終えて次の工程へ送られるまでの一連の動きを、一つひとつの作業単位で細かく書き出します。それぞれの作業に「何分かかっているか」「誰が担当しているか」を記入していくと、「この作業と次の作業の間で待ち時間が長い」「AさんとBさんが同じような確認を二重に行っている」といった問題点が面白いように浮かび上がってきます。
DX推進による工数管理の効率化
検査の自動化は、単なる部分的な効率化ではなく、会社全体の仕事のやり方を変えるDX(デジタルトランスフォーメーション)の一環として捉えるべきです。自動検査システムから得られる合否判定や寸法データといったデジタル情報を、工場の生産状況を管理するシステム(MES)や、品質情報を管理するシステム(QMS)とつなげることが大切です。この連携によって、これまで担当者が手で集計し、エクセルなどで報告書を作成していた工数や不良率の管理が全自動になります。その結果、管理業務にかかっていた時間が劇的に減り、品質の状態をリアルタイムでグラフなどにして確認できるため、問題が起きた際の素早い判断にも繋がります。
ROI(投資対効果)の可視化方法
自動化に踏み切るかどうかの最終判断には、「ROI(アールオーアイ/投資対効果)」の計算が欠かせません。これは簡単に言うと、「かけた費用に対して、どれだけの見返りがあるか」を示す指標です。最も分かりやすい見返りは、自動化によって削減できた検査の人件費でしょう。しかし、自動化の効果はそれだけではありません。不良品が外部に流出するのを防ぐことによるクレーム対応費用の削減や、品質が向上することによる会社のブランドイメージアップ、検査データを分析して不良の原因を突き止め、製品全体のロスを減らす効果なども、見返りに含めて考えるべきです。これらの効果をなるべく金額に換算し、「投資したお金を何年で取り戻せるか」を具体的に示すことが、社内の合意を得るための重要な鍵となります。

生産性向上に繋げるための自動化活用法
検査ミス低減・品質安定の仕組み作り
本当の意味での生産性向上は、単に作業スピードを速めることだけを指すのではありません。不良品を作ってしまい、後から手直ししたり、廃棄したりする無駄をなくすことが、本質的な生産性の向上です。自動検査システムは、決められた客観的な基準で、24時間休むことなく安定して検査を実行します。人の目と違って「うっかりミス」や「判断のブレ」がありません。この仕組みが、不良品の市場への流出を根本から防ぎ、製品の品質を高いレベルで安定させます。その結果、顧客からのクレームが減り、再検査や追加生産といった余計なコストと時間がかからなくなるため、工場全体の生産性が大きく向上するのです。
自動化でできるリアルタイムデータ活用術
検査の自動化は、膨大なデジタルデータを生み出す「宝の山」です。このデータを「リアルタイム」、つまり“今まさに起きていること”として活用することで、生産性を飛躍的に高めることができます。一つの活用法として、特定の不良品の発生率が急に上がった場合に、即座に管理者のスマートフォンやPCにアラート(警告)を送る仕組みが考えられます。異常をいち早く察知し、すぐに対応できるため、大量の不良品を作り続けてしまう事態を避けられます。また、蓄積されたデータを分析し、「この機械で加工した部品は不良が出やすい」といった傾向を掴めば、機械のメンテナンス計画や、より良い製造方法の検討に役立てることも可能です。
ライン全体のボトルネック解消法
生産ライン全体の能力は、実はその中で最も作業に時間がかかる工程(これを「ボトルネック」と呼びます)の能力で決まってしまいます。高速道路で一車線だけ工事中だと、全体が渋滞してしまうのと同じ原理です。多くの場合、人の手による複雑な検査工程がこのボトルネックとなり、ライン全体のスピードを制限しています。ここに高速な自動検査システムを導入することで、渋滞が解消され、ライン全体がスムーズに流れるようになります。結果として、生産能力そのものが向上します。自動化を計画する際は、まず自社のラインのどこがボトルネックになっているかを正確に見極め、そこを優先的に改善することが、最も効果の高い投資となるでしょう。
AI外観検査の活用と進化
AI技術の進化は、外観検査の世界に革命をもたらしています。従来の画像処理では、「長さが〇mm以上、色がこの範囲から外れたら不良」といったように、不良の条件を人間が細かく数値で設定する必要があり、その調整には多くの手間と経験が必要でした。これに対しAI外観検査は、たくさんの良品と不良品の画像を見せるだけで、AI自身が「何が良い状態で、何が悪い状態か」の特徴を学習します。このおかげで、熟練者の「感覚」でしか判断できなかったような、金属の光沢のムラや布の風合いの違いといった曖昧な不良も、高い精度で判別できるようになってきています。
トレーサビリティと情報共有の強化
自動検査システムは、検査した全ての製品について、「いつ、どのラインで、どんな基準で検査し、結果はどうだったか」という詳細な履歴を、デジタルデータとして自動で記録します。製品一つひとつに割り振られた番号とこの検査データを結びつけることで、「トレーサビリティ(追跡可能性)」が確立されます。これは、万が一、市場に出た製品に問題が見つかった場合でも、その製品がいつどこで作られたものかを瞬時に特定し、迅速な回収や原因究明を可能にする非常に重要な仕組みです。また、この検査データは社内のネットワークを通じて関係部署とすぐに共有できるため、品質改善に向けた話し合いや対策もスピーディーに進みます。
検査自動化導入の進め方と注意点
現場でよくある失敗とその回避策
検査自動化の導入で陥りがちな失敗が、「カタログスペックだけを見て高性能なシステムを選んだのに、いざ現場に設置したらうまく動かない」というケースです。その多くは、現場の環境や実際の運用を考えていなかったことが原因です。粉塵が舞う工場なのに防塵対策が甘いカメラを選んでしまったり、操作画面が複雑すぎて現場の作業員が扱えなかったりといった例が後を絶ちません。
こうした事態を避けるには、計画の最初の段階から、実際にシステムを使う現場の担当者をプロジェクトチームに加えることが何よりも大切です。現場の生の声や困りごとを吸い上げ、それをシステムの仕様にしっかり反映させることで、導入後の「こんなはずじゃなかった」を防げます。
スモールスタートから始めるポイント
最初から工場全体の検査を一度に自動化しようとすると、非常に大きな投資とリスクを伴います。成功への近道は「スモールスタート」、つまり小さく始めてみることです。まずは、最も課題が大きいと感じている一つの工程や、特に不良が多くて困っている製品に絞って、試験的に導入してみましょう。小さな成功を体験することで、自動化を進めるためのノウハウが社内に溜まり、周囲の協力も得やすくなります。この最初のプロジェクトで得た学びや反省点を元にして、次のステップ、その次のステップへと、少しずつ範囲を広げていくやり方が、着実な成功への道筋です。
社内人材育成・スキルアップ方法
自動化システムが導入されると、これまで検査を担当していた人の役割も変わります。単純な目視作業から、導入されたシステムの操作や日々のメンテナンス、そして集まった検査データを分析して改善案を考えるといった、より高度な仕事が求められるようになります。会社側は、こうした変化に対応できるよう、従業員のスキルアップを計画的に支援する必要があります。具体的には、システム会社の研修に従業員を派遣したり、データ分析の基本を学ぶ社内勉強会を開いたりすることが考えられます。自動化を「仕事を奪うもの」と捉えるのではなく、「新しい能力を身につけるチャンス」と位置づけ、従業員の成長を後押しする姿勢が大切です。
外部パートナーとの連携・委託のコツ
自社の力だけで、高度な自動化システムの設計から構築、運用まで全てを行うのは、多くの場合で現実的ではありません。そこで重要になるのが、信頼できる外部の専門家(システムインテグレータや専門商社など)との協力です。良いパートナーを選ぶ際は、単に製品の価格や性能だけでなく、「自分たちの業界や製品について詳しいか」「導入後に困ったときのサポート体制はしっかりしているか」といった点を重視しましょう。
また、契約を結ぶ前に、「どこまでを自分たちで行い、どこからを専門家にお願いするのか」という役割分担を、文書ではっきりとさせておくことが、後の「言った・言わない」のトラブルを防ぐために不可欠です。
費用対効果を最大化する導入ステップ
費用対効果を最大にするには、計画的なステップを踏むことが成功の鍵を握ります。
ステップ1:現状分析と課題の明確化。 まずは仕事の流れを図に描くなどして現状を「見える化」し、どこに一番の問題があるか、どこを改善すれば最も効果が出るか、ターゲットを絞ります。
ステップ2:要件定義とパートナー選定。 解決したい課題を元に、システムに必要な機能や性能を具体的にリストアップし、それを実現できる最適なパートナーを探します。
ステップ3:PoC(ポック/概念実証)の実施。 本格導入の前に、実際の製品を使って小規模な「お試し」運用を行います。ここで、本当に効果があるのか、技術的に問題ないかを確認します。
ステップ4:導入と効果測定。 小さな範囲で本番導入を開始し、投資した費用に対してどれだけの効果が出たかを具体的に数値で測定します。
ステップ5:水平展開。 最初の成功モデルを、他のラインや工場へと同じように展開していきます。
今後の検査自動化と生産現場の未来展望
AI・IoT・ロボットの融合がもたらす革新
これからの検査自動化は、AI、IoT(モノのインターネット)、ロボットがさらに賢く連携することで、想像を超える革新を生み出します。工場の機械に取り付けられたIoTセンサーが、機械のわずかな振動や温度の変化を常に監視し、その情報をAIが分析。「このままだと不良品が出始めるかもしれない」という“予兆”を捉え、ロボットが自動で機械の調整を行う、といった「予知保全」が当たり前になります。検査は、もはや出来上がった不良品を見つける「出口管理」から、不良品そのものが生まれないようにする「源流管理」へと、その役割を変えていくのです。
グローバルで進む自動化最新トレンド
世界に目を向けると、検査の自動化は「スマートファクトリー」や「インダストリー4.0」といった、より大きな構想の中で進化しています。これは、工場内のあらゆる機械やシステムをインターネットでつなぎ、集めた膨大なデータをAIで解析して、工場全体の動きを最適化しようという考え方です。いわば、工場そのものを一つの「考える生き物」のようにしてしまう取り組みです。この仕組みによって、複数の国の工場で生産される製品の品質を、リアルタイムで同じレベルに保つことも可能になります。こうした世界の最新の動きを常に把握し、自社の戦略にどう活かせるかを考える視点が、これからの競争には欠かせません。
脱属人化と組織全体の底上げ
検査自動化が目指す最終的なゴールは、単に人を減らすことではなく、「脱属人化」を通じて組織全体の力を高めることです。これは、特定のスーパーマン的な熟練検査員一人の「匠の技」に頼る状態から抜け出すことを意味します。これまで個人の頭の中にしかなかったノウハウや勘が、AIやシステムという誰もが共有できる「会社の財産」に変わります。この変化が、組織として安定した品質保証体制を築く土台となります。また、単純作業から解放された従業員は、より創造性が求められる改善活動などに時間を使えるようになり、組織全体のスキルと仕事への意欲を高めることにも繋がります。
環境・SDGs対応と自動化の関係性
検査の自動化は、実は地球環境への配慮や、SDGs(持続可能な開発目標)といった社会的な課題への貢献にも繋がっています。精度の高い検査で不良品の発生を減らし、歩留まり(良品率)を高めることは、製品の廃棄ロスや、作り直しにかかる電力などのエネルギー消費を直接的に削減します。これは、SDGsが掲げる目標の一つ「つくる責任 つかう責任」を、企業活動の中で実践する具体的なアクションです。また、検査データを活用して生産プロセス全体を効率化することは、工場全体の省エネルギーにも貢献し、企業の環境負荷を低減させます。
人と機械が共創するこれからの生産現場像
検査の自動化が当たり前になった未来の工場から、人の姿が消えるわけではありません。むしろ、そこには「人と機械が、それぞれの得意なことを活かし合って協力する」という新しい姿があります。スピード、精度、持久力といった面は機械がその能力を最大限に発揮し、人間は、機械では難しいイレギュラーな事態への対応、より良い生産方法を考える創造性、そしてシステム全体を管理・監督するという、より高度な役割を担います。機械を最高のパートナーとして、ものづくりの本質を探求していく。そんな、人が主役であり続ける生産現場こそが、私たちが目指すべき未来です。
まとめ:未来の製造業を切り拓く、戦略的な検査自動化への一歩
この記事では、検査業務の自動化がもたらす大きなメリットと、その導入を成功に導くための具体的な考え方や手順について解説しました。人手不足という大きな波と、ますます高まる品質への要求に応えていくために、自動化はもはや選択肢の一つではなく、企業の未来を左右する重要な戦略です。
工数削減や生産性向上といった目に見える効果はもちろん、個人への依存から脱却した強い組織作りや、データ活用による絶え間ない改善活動など、その恩恵は計り知れません。まずは自社の課題を正しく見つめ、小さな一歩を踏み出すことが、未来の工場を創造する、何より確実な方法となるはずです。
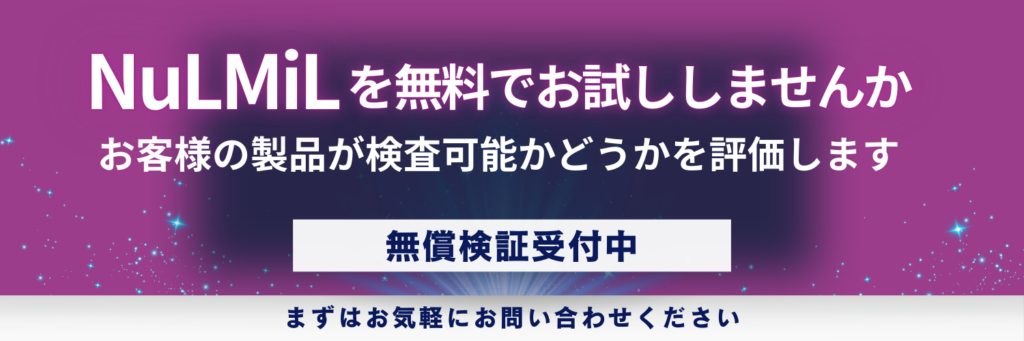