背景
プラスチック製品製造企業では、プラスチック製品(箱型製品)の品質管理において、汚損・破損・シール残り・白化といった欠陥の検査を行っていました。従来は、洗浄後に別作業をしながら、作業員が目視で検査を実施していましたが、以下のような課題がありました。
- 検査と別作業を同時に行うことで、見落としのリスクが高い
- 人手不足により、検査作業に十分なリソースを割けない
- 1日あたりの生産量が増加し、従来の目視検査では処理が追いつかない
- 検査作業の工数を削減し、効率化を図りたい
これらの課題を解決するため、企業はインライン検査システムの導入を進めることになりました。
導入したシステム
門型の画像検査装置をコンベアに組み込むインライン検査システムを採用しました。このシステムでは、以下の流れで検査が行われます。
- コンベアを流れるプラスチックコンテナをカメラで撮影
- AIを活用した画像解析システムが、リアルタイムで判定
この仕組みにより、作業員が別作業をしながら検査する手間を削減しました。
導入の成果
インライン検査に移行したことで、作業中の目視検査の必要がなくなり、作業負担が軽減。また、人手不足の中でも安定した検査が可能となり、品質管理の精度が向上しました。加えて、生産ラインの流れを止めることなく検査を行えるため、作業効率が大幅に向上しました。
導入にかかったコストは以下の通りです。
- 既存コンベアに組み込み型の画像検査システムを導入:1300万円~1900万円
- 人件費削減と作業効率化により、長期的に見て大きなコストメリットにつながる
今後の展望
今回の導入成果をもとに、企業では他の製品ラインにも同様のインライン検査システムを展開する計画を立てています。また、AIの学習精度向上や検査データの分析強化により、さらなる品質向上と生産性向上を目指しています。
当社の外観検査システムは、人手不足や品質管理の課題を抱える企業様にとって、効率的な解決策となります。今後も、製造業の検査業務を支える技術開発を進めてまいります。
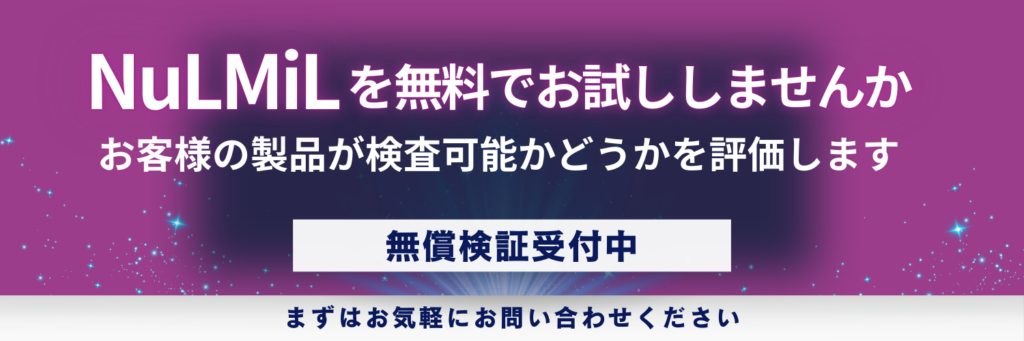