歩留まりの重要性とその背景
製造現場において「歩留まり」は、原料や素材に対してどれだけの完成品(良品)が得られるかを示す重要な指標です。企業の利益や生産性、品質管理、さらにはコスト削減にも直結するため、現場の従業員だけでなく経営層にも理解が求められます。歩留まりが高いということは、無駄なく効率的な生産が行われている証拠であり、逆に低い場合は不良品の多発や工程上のロスが企業全体の競争力を損なう可能性があります。この記事では、歩留まりの意味、計算方法、そして具体的な改善策について詳しく解説します。
製造現場における歩留まりとは?
歩留まりの定義と語源
歩留まりとは、原材料や投入資源に対して、最終製品として出荷できる良品の割合を示す指標です。つまり、製造工程でどれだけ無駄がなく、効率的に製品を生産できたかを数値化するものです。歩留まりが高い場合、原材料やエネルギー、作業時間が効率的に活用されていることを意味し、逆に低い場合は不良品の発生や工程上のロスが多いことを示します。
歩留まりは、製造現場における品質管理やコスト削減のための重要な管理項目であり、企業全体の競争力向上にも大きく影響します。歩留まりの数値を正確に把握し、その改善に取り組むことで、無駄なコストの削減、納期の短縮、さらには市場における信頼性の向上が期待できます。
良品率との違い
歩留まり率は、原料に対する完成品の割合を示すのに対し、良品率は完成品の中で不良品が除かれた良品の割合を意味します。両者は密接な関係があり、歩留まり率が低下すれば、良品率も悪化し、結果として企業全体の収益に悪影響を与えることになります。
歩留まりの計算方法と具体例
基本的な計算式
歩留まり率は、以下のシンプルな計算式で求められます。
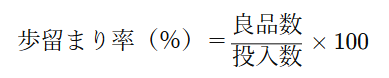
また、不良品数が分かる場合は次の式も利用できます。
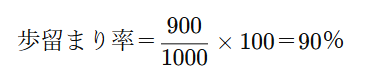
たとえば、1000個の部品を投入して900個の完成品が得られた場合、歩留まり率は90%となります。この計算は、製造工程全体の効率性を客観的に評価するための基本となります。
各工程ごとの歩留まり分析
製造ラインが複数工程に分かれている場合、各工程ごとに歩留まり率を計測する「工程歩留まり」を導入することで、どの工程に問題が潜んでいるかを特定できます。工程ごとの不良品数を正確に把握し、ボトルネックやヒューマンエラー、設備トラブルなどの原因を分析することが、全体の歩留まり向上には不可欠です。
歩留まりが高いと、良品が多く生産され、不良品がほとんど発生しない場合、歩留まり率は100%に近づいていくことになります。これは、製造現場が効率的であると同時に、品質管理が徹底されている証です。歩留まりが低い状態では不良品が多発する場合、歩留まり率が低下し、原料費や製造コストの無駄が発生します。これは企業の利益を圧迫し、競争力の低下につながるため、迅速な対策が求められます。
歩留まり低下の原因は…
歩留まり率の低下は、現場の様々な要因が複合的に影響して生じます。まず、作業者のミスが大きな原因となるケースがあり、部品の取り付けや操作の誤りが生産管理の不備を示唆します。こうしたヒューマンエラーは、教育体制や作業手順の見直しが求められる要因です。また、長期間使用された製造設備の老朽化も品質低下の原因となります。設備の劣化は、製品の安定した生産を妨げ、不良品の増加に直結します。定期的なメンテナンスと設備更新が不可欠です。
さらに、製造プロセス自体の不備や、整備されていない作業マニュアルも歩留まり率を下げる要因です。工程ごとの標準化が進んでいないと、作業のばらつきが発生し、品質が不安定になります。加えて、製品設計の問題や原材料の品質低下も、不良品の発生に影響を及ぼすため、初期段階での検証が重要です。これらの要因を踏まえ、特にヒューマンエラーの徹底的な原因追及が求められます。部品の取り付けミスや操作ミスが多発している場合は、生産管理体制の見直しや現場教育の強化が必要です。全体として、設備の点検、工程の標準化、原材料の選定など、各要素の改善が歩留まり率向上につながると言えるでしょう。
歩留まり率の改善方法と実践例
歩留まり率を改善するためには、原因分析から具体的な対策まで一連の取り組みが必要です。ここでは、実際の製造現場で実践できる改善方法をいくつか紹介します。
1. 適切な目標を設定
まずは現実的な目標値を設定し、達成すべき改善指標を明確にします。これにより、関係者全員が共通の目的に向かって取り組むことが可能となります。たとえば、前四半期と比較して歩留まり率を10〜15%向上させる目標を定めると、具体的な改善活動に繋がります。
2. 不良原因の究明と対策
各工程で発生している不良品の原因を詳細に分析し、改善策を講じることが重要です。工程ごとのデータを収集し、ヒューマンエラー、設備の問題、原材料の品質など、どこに問題があるのかを正確に把握します。これには、現場でのヒアリングや統計的手法、さらにはAIやIoTセンサーを活用したリアルタイムモニタリングが効果的です。
3. 設備の定期点検と最新化
製造設備の老朽化は歩留まり低下の大きな原因のひとつです。定期的なメンテナンスを実施し、必要に応じて最新の自動化設備やAIによる異常検知システムを導入することで、工程のばらつきを抑えることができます。最新技術の導入は、生産性向上とともに不良品削減にも寄与します。
4. オペレーター教育と作業標準の徹底
製造現場でのヒューマンエラーを防ぐため、オペレーターに対する定期的な教育や技能訓練は欠かせません。標準作業手順書(SOP)の整備と徹底は、不良品の発生を防ぐための基本です。また、直行率(一発合格の良品の割合)をチェックすることで、再加工の手間を減らし、品質の安定化が期待されます。
5. プロセスの標準化とPDCAサイクルの活用
製造工程全体のばらつきをなくすために、作業手順や工程を標準化することが必要です。PDCAサイクル(計画・実行・評価・改善)を取り入れ、定期的にプロセスの改善活動を実施することで、歩留まり率の持続的な向上が可能となります。
6. AI・IoTセンサーの活用によるリアルタイム監視
近年、AIやIoTセンサーを活用したスマートファクトリー化が進んでいます。生産工程に設置されたセンサーからリアルタイムでデータを収集し、AIがそのデータを解析することで、不良品発生の予兆を早期に検知するシステムが実現されています。これにより、異常が発生した際の迅速な対応が可能になり、全体の歩留まり率向上につながっています。
7. サプライチェーン全体の見直し
歩留まり率は、製造現場だけでなく、原材料や部品の品質にも大きく依存します。サプライヤーとの連携を強化し、納入前の検査や品質管理を徹底することで、初期不良の発生を抑え、全体の歩留まりを改善することができます。
実際の現場では、上記の改善策を組み合わせることで、歩留まり率の大幅な向上が実現されています。今後、製造現場ではさらなる自動化とデジタル技術の進化により、リアルタイムな品質管理がますます重要となります。歩留まり率の向上はもちろん、生産性の飛躍的な向上やコスト削減が期待され、企業全体の競争力向上に寄与することでしょう。
まとめ
製造現場における歩留まりは、品質管理、生産性向上、コスト削減、さらには企業の収益に直結する極めて重要な指標です。歩留まりの計算方法や原因を正確に把握し、AIやIoTセンサーなどの最新技術を活用した改善策を実施することで、現場全体の効率性を向上させることが可能です。適切な目標設定、徹底した原因分析、設備更新、オペレーター教育、プロセスの標準化、そしてサプライチェーン全体の見直しといった取り組みが、歩留まり改善の鍵となります。
これらの施策を総合的に実施することで、品質の安定化とコスト削減を実現し、競争力を高めることができます。製造現場における歩留まりの改善は、一朝一夕に実現できるものではありませんが、継続的な改善活動を通じて、スマートファクトリーの実現に向けた大きな一歩となるでしょう。今後も、最新技術と現場の知恵を融合させ、歩留まり率の向上とともに、効率的で持続可能な生産体制を築いていくことが求められます。
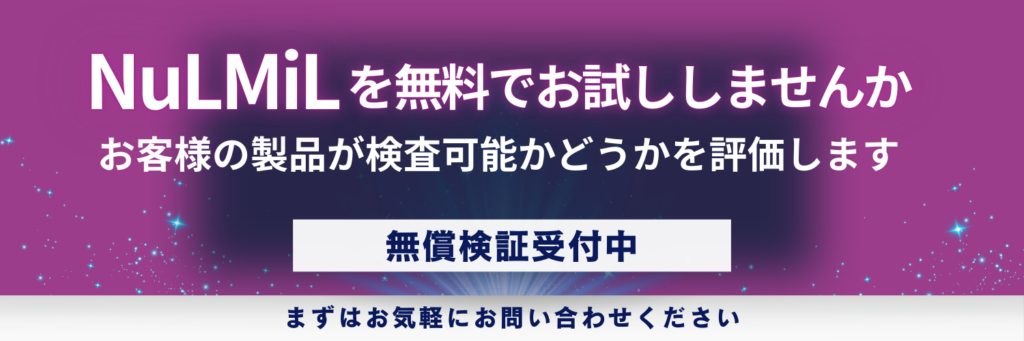