製造現場では、生産ラインが停止すると大きな損失につながります。短時間の停止であっても、頻繁に発生すると累積で大幅なロスとなってしまいます。このような短時間の停止は「チョコ停」と呼ばれています。センサーの誤作動や作業ミスによる数分から十数分の停止が繰り返されることで、結果的に稼働率が低下してしまいます。
一方で、長時間にわたるライン停止を「ドカ停」と呼びます。これは大規模な故障やメンテナンスによって発生し、企業の生産活動に甚大な影響を及ぼします。チョコ停とドカ停は停止の規模こそ異なりますが、いずれも対策を怠ると大きなリスクにつながるという点では共通しています。本記事では、チョコ停の定義やドカ停との違い、発生原因、現場への影響、そして具体的な対策について解説します。
チョコ停:短時間停止 ドカ停:長時間の停止
チョコ停は、数分から十数分の短時間停止を指し、一日に複数回発生すると合計の停止時間が意外なほど長くなってしまいます。例えば、センサーの誤検知でラインが停止したり、作業員が備品を取りに行くために一時的にラインを止めたりするケースが挙げられます。こうした些細な要因が重なることで、生産能力の低下につながります。特に、多品種少量生産を行う現場や、頻繁に段取り替えを行うラインでは、細かなトラブルが増えるためチョコ停が発生しやすい傾向にあります。
チョコ停とは異なり、ドカ停は1時間以上、場合によっては半日以上ラインが停止する深刻なケースを指します。機械の大きな故障やシステムトラブルなどが主な原因となります。チョコ停は短時間で復旧可能ですが、その回数が増えると最終的にはドカ停と同程度の生産ロスにつながる可能性があります。
チョコ停がもたらす現場への影響
チョコ停が頻発すると、稼働率が低下し、生産効率が落ちます。ラインが一度停止すると、再起動のための調整や確認作業が必要になるため、その間の生産量が減少します。また、これを補うために残業や追加の人員配置が求められ、コストの増加につながります。
さらに、チョコ停が発生すると、ライン上のワーク(加工途中の製品)が中途半端な状態で残ることがあります。温度や湿度に影響されやすい製造工程では、これが原因で材料が劣化し、品質不良につながる可能性があります。最終検査で不良品を発見できたとしても、再加工や廃棄コストが発生し、生産効率の悪化を招く恐れがあります。
また、頻繁なチョコ停は、作業員にとって大きなストレスとなります。作業の流れが途切れることでモチベーションが低下し、集中力も維持しづらくなります。短時間の停止と再開を繰り返すことで疲労が蓄積し、新たなミスを誘発する悪循環に陥る可能性もあります。
チョコ停を引き起こす主な原因
チョコ停の主な原因の一つは、設備やセンサーのわずかな不調です。例えば、センサーにホコリや油が付着すると感度が低下し、誤作動を引き起こしてラインが停止することがあります。また、駆動部品の摩耗や潤滑油の不足なども小さな異常を発生させ、結果的にチョコ停の原因となることがあります。
他に、作業員の手順ミスや準備不足によってラインを一時停止しなければならないケースも多くあります。作業標準が不明確な場合や、教育が行き届いていない現場ではミスが発生しやすくなります。
ラインの稼働状況をリアルタイムで把握できないと、チョコ停の発生を見逃し、改善が後手に回ってしまいます。停止時間や原因を記録・管理する仕組みがなければ、適切な対策を講じるのが難しくなります。
チョコ停の対策とドカ停への発展予防
チョコ停の発生を軽視せず、稼働データを記録・分析することが重要です。PLC(プログラマブルロジックコントローラ)やIoTシステムを活用し、リアルタイムでラインの稼働状況を監視することで、停止パターンの分析と改善策の立案が可能になります。
また、センサーの定期清掃や潤滑油の交換、部品の摩耗チェックなど、予防保全を徹底することで、チョコ停の発生を最小限に抑えることができます。
作業標準を文書化し、作業員がどの手順でも同じ動作を行えるようにすることで、人為的なミスを減らすことができます。段取り替えの効率化を図り、必要な工具や材料を事前に準備することでチョコ停の発生を防ぐことができます。
AIと自動化によるチョコ停低減の可能性
AIを活用した外観検査システムを導入することで、人間の目視検査を減らし、検査のたびにラインを止める必要がなくなります。リアルタイムでの品質チェックにより、不良品の流出も防ぐことができます。
さらに、AIを活用した予兆検知システムにより、センサーからのデータを常時監視し、異常を早期発見することで、チョコ停を未然に防ぐことができます。
まとめ:ドカ停へつながるチョコ停の危険性
チョコ停は小さな問題のように見えますが、放置すれば累積的な損失を生むだけでなく、ドカ停に発展するリスクもあります。稼働データの可視化、設備保全の徹底、作業標準の整備、AI技術の活用など、具体的な対策を講じることで、生産効率と品質を維持しつつ、停止リスクを最小限に抑えることが可能となります。
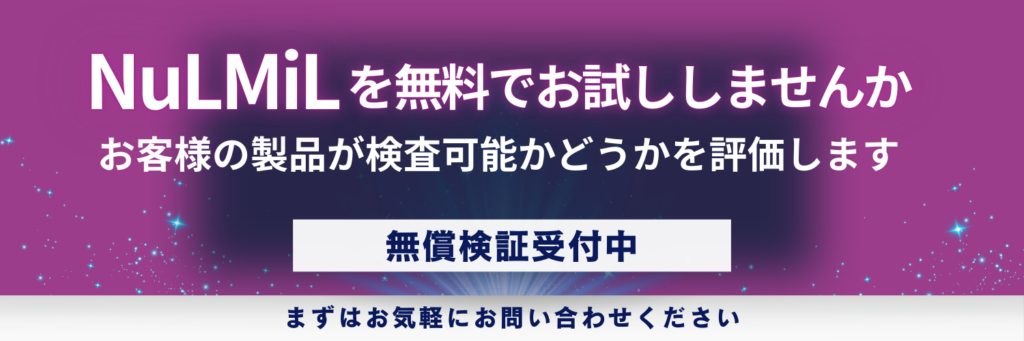