なぜ画像検査における照明選定が重要なのか?
画像検査の精度は、照明の選定と設定によって大きく左右されます。適切な照明を使用しないと、以下のような問題が発生し、検査の信頼性が低下します。
問題 | 影響 | 発生する可能性のあるトラブル |
---|---|---|
影の発生 | 欠陥が一部見えなくなる | 傷や異物を見落としてしまう |
反射の影響 | 画像の一部が白飛びしてしまう | 金属や光沢面の欠陥検査が困難になる |
照明ムラ | 画像の明るさが不均一になる | AI・画像処理が誤検出を起こす |
波長の選定ミス | コントラストが不足する | 欠陥と正常部の差が不明瞭で誤判定が増える |
環境光の影響 | 外部光により対象が見えづらくなる | 誤検知や検査結果のバラつきが生じる |
以上のように、照明は検査対象の欠陥を際立たせ、カメラが捉えやすい画像を得るために欠かせない要素です。本記事では、照明の種類や波長、照射角度、配置方法について体系的に解説し、最適な選定・調整方法を紹介します。
影の発生が検出精度に及ぼす影響
検査対象に照明を当てる際に影が生じると、欠陥の一部が暗く隠れてしまい、カメラが検出できなくなります。例えば表面の微細なキズや異物が影に紛れ、見落としに繋がる恐れがあります。適切な照明角度と複数光源の配置で影を抑えることが重要です。
反射による誤検知のリスク
金属や光沢のある素材では、照明の反射によって画像の一部が極端に明るく映る(白飛びする)ことがあります。眩しすぎる反射光はカメラのセンサーを飽和させ、欠陥の輪郭を隠してしまいます。その結果、本来あるべき欠陥を検出できずに誤判定するリスクが高まります。
照明ムラが招く検査の不安定さ
照明にムラ(明るさの偏り)があると、画像内で明るい部分と暗い部分が生じ、検査アルゴリズムの判断が不安定になります。明るさのばらつきはAIや画像処理の誤検出を招き、正常品を不良と判定したりその逆を見逃したりする原因となります。安定した検査には均一な光を照射する工夫が必要です。
不適切な波長選択によるコントラスト低下
照明の波長(光の色)が対象に適していないと、欠陥と背景とのコントラストが十分得られません。例えば、対象物と同じ色の光で照らすと欠陥が背景に溶け込み、判別しにくくなります。波長選定を誤ると欠陥と正常部分の差が不明瞭になり、検出漏れや誤検知が増加します。
環境光が検査に及ぼす影響
工場内の天井照明や外光などの環境光が検査エリアに入り込むと、照明条件が一定せず検査画像にばらつきが生じます。外光によるグレア(ちらつき)や日照変化によって、同じ欠陥でも検出できたりできなかったりとムラが発生しかねません。検査専用の照明環境を整えないと、せっかく選んだ最適な光源の効果が十分発揮されなくなります。
1. 画像検査に適した光源の種類
検査に用いる照明の種類は、検査対象の材質や検出したい欠陥の種類によって選び分ける必要があります。ここでは主な光源の種類とその特徴、適用例を示します。
光源の種類 | 特徴 | 主な適用例 |
---|---|---|
LED照明 | 長寿命・省エネで色や形状のバリエーションが豊富。発熱が少なく制御が容易。 | 一般的な外観検査全般(金属部品のキズ、樹脂製品の欠陥など) |
蛍光灯照明 | 広範囲に均一な光を照射できるが寿命が短く、チラつきが発生することも。 | ラベル印刷や紙製品の検査、食品包装の外観チェック |
ハロゲン照明 | 可視光を連続スペクトルで放射し自然光に近い光質。ただし発熱が大きい。 | 色調や外観の色むら検査(塗装の色確認、食品の鮮度評価) |
レーザー照明 | 指向性が非常に高く、細い線状光やスポット光で特定部分を強調可能。 | 3D寸法測定(レーザ変位)、微細な傷や微小異物の検出 |
UV・IR照明(紫外線・赤外線) | 人の目には見えない特殊光。UVは対象を蛍光させて微細欠陥を可視化、IRは素材を透過して内部欠陥を検出。 | UV:ひび割れ・塗装剥離の検出、IR:食品・プラスチック内部の異物検査 |
LED照明
LED照明は現在最も汎用性が高く主流となっている光源です。低消費電力かつ長寿命で、赤外線や紫外線を含む様々な色のLEDが利用可能なため、幅広い検査ニーズに対応できます。また、小型化しやすくリング状・バー状・面状など多彩な形状の照明が製作可能な点も特長です。
蛍光灯照明
蛍光灯照明は広い範囲を均一に照らせますが、点滅(フリッカ)が発生しやすく寿命も短い欠点があります。かつて主流でしたが近年はLEDへの置き換えが進んでおり、特殊用途を除き使用頻度が減っています。
ハロゲン照明
ハロゲンランプは太陽光に近い連続光スペクトルを持ち、色の識別が必要な検査に有効です。しかし発熱と消費電力が大きいため、光源の熱影響や寿命にも注意が必要です。
レーザー照明
レーザー照明はスポット的に非常に強い光を当てられるため、ごく小さなキズの検出やレーザー変位計による3D計測などに活用されます。ただしレーザー光は目に有害となる可能性があり、安全管理や光学系の調整も難しいため、用途は限定されます。
UV・IR照明
紫外線(UV)照明は特殊なコーティング欠陥を蛍光で浮かび上がらせたり、蛍光剤を使った検査に利用できます。赤外線(IR)照明は可視光では見えない内部の異物や構造を検出する際に有効です。なおUVやIRを用いる場合、カメラ側も対応波長のセンサーやフィルターを備える必要があります。
2. 波長(色温度)による照明選定とコントラスト最適化
照明の波長(光の色、色温度)を変えると、対象物の見え方や欠陥とのコントラストが大きく変化します。適切な波長を選ぶことで、欠陥を背景から際立たせ、検出精度を向上させることが可能です。以下に代表的な光の色と特徴、適した用途を示します。
光の色(波長) | 特徴 | 主な適用例 |
---|---|---|
白色光(標準) | 可視光の全波長を含むバランスの良い光。人間の目で見た色に近い。 | 汎用的な外観検査全般(食品、金属、プラスチック製品など) |
赤色光(約630nm) | 波長が長く金属表面のギラつきを抑えやすい。コントラスト向上効果。 | 金属加工品のキズ検出、プリント基板上の文字・パターン検査 |
青色光(約470nm) | 波長が短く微小な傷を強調。透明体のキズや異物を目立たせる効果。 | ガラス・フィルムの傷検出、樹脂内の気泡や異物検査 |
赤外線(IR:約850nm) | 可視光より長波長で素材を透過しやすい。表面下の情報を取得可能。 | 食品やプラスチック容器内部の異物検出、封入物の確認 |
紫外線(UV:約365nm) | 人には見えない短波長。蛍光を発する物質を可視化し欠陥を浮出。 | コーティングの割れ検出(蛍光塗料使用)、紙幣・印刷物の真贋検査 |
白色光
白色光は可視光の全波長を含むバランスの良い照明で、対象物の色味を自然に再現できます。そのため外観検査において基準としてまず使用されることが多い光です。しかし特定の欠陥を強調したい場合、単色光(カラー照明)の方が有利なケースもあります。
赤色光
赤色光は波長が長いため鏡面反射の影響を抑えやすく、金属表面検査でよく用いられます。表面のキズによる微小な反射差を捉えやすいため、金属の傷を背景から浮かび上がらせるのに適しています。
青色光
青色光は波長が短いため微細構造での光の散乱が増え、透明なフィルム上の微小な塵や傷も浮かび上がりやすくなります。ガラスや樹脂製品の微小欠陥検出に効果を発揮します。例えば青色LEDでプラスチックフィルムを照らすと、微細な埃が散乱光で白く光り、欠陥を見つけやすくなります。
赤外線(IR)照明
赤外線照明(IR)は可視では見えない内部の異常検知に有効で、例えば果物内部の傷みやプラスチック容器内の異物を透過撮影で見つけることができます。ただし赤外線は通常カメラのセンサーでは白黒像として捉えられるため、可視光とは異なるコントラストになる点に注意が必要です。
紫外線(UV)照明
紫外線照明(UV)はそれ自体で対象を映すというより、対象物が発する蛍光を可視化する手法に使われます。UVを当てると特定の材料や汚染物が光るため、肉眼や通常の照明では見えない微細なクラック(ひび)や汚れを検出できます。なお欠陥によっては、可視光とこれら不可視光を組み合わせて用いることで検出精度が一層向上する場合もあります。
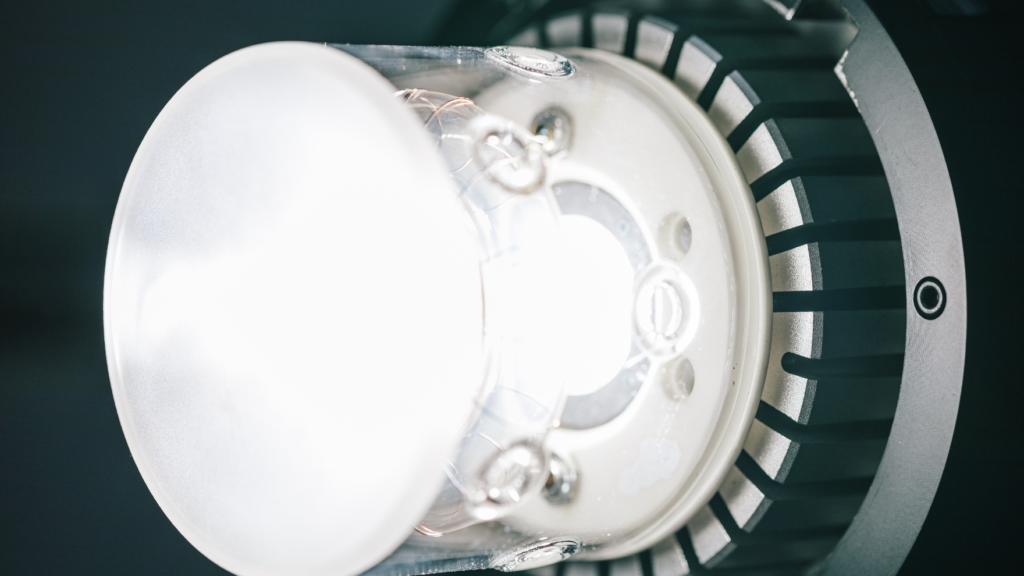
3. 照明の方向(入射角)の選び方
光の当て方(入射角度)を工夫すると、同じ対象でも見え方が大きく変わり、欠陥の視認性を高めることができます。照明をどの方向から当てるかによって、いわゆる「明視野」(正反射光をカメラが捉える照明)にも「暗視野」(拡散反射光のみ捉える照明)にもなり、欠陥を白く浮かび上がらせるか黒く沈み込ませるかを制御できます。代表的な照明手法の特徴と用途を以下にまとめます。
照明手法 | 特徴 | 主な適用例 |
---|---|---|
直射照明 | カメラに向けて真っ直ぐ光を当てる明視野照明。全体を明るく照らすが影もできやすい。 | 印刷物やパッケージなどフラットな対象の表面検査 |
拡散照明 | 光を一度拡散板やドームで乱反射させて柔らかく照射。影やグレアを低減。 | ガラス・樹脂など反射しやすい素材の表面検査 |
斜光照明 | 対象に対し浅い角度から斜めに当てる暗視野照明。微小な凹凸を強調。 | 金属表面のキズや打痕の検出、基板パターンの段差検査 |
同軸照明 | カメラと同じ軸上から半透明ミラーを介し照射する明視野照明。正反射のみ捉える。 | 鏡面仕上げ部品の傷・汚れ検査、印刷文字の照査 |
ドーム照明 | 半球状の内壁で全方向から均一照射する拡散照明。あらゆる方向の影を皆無に。 | 曲面や凹凸を持つ光沢物体の検査(自動車部品など) |
直射照明
直射照明はリングライトなどを用いて上方から直接照らす方式で、検査対象全体を明るく照らします。ただし表面に凸凹があると陰影がくっきり出てしまい、小さな欠陥が陰に隠れることもあります。
拡散照明
拡散照明は、照明に拡散フィルムやドーム型の光学部品を使って、一度光を乱反射させてから当てる方法です。これにより光沢面で生じるギラつき(ハレーション)を抑え、均一な明るさで対象を照らせます。ガラス板やディスプレイなど反射率の高い対象物の検査で威力を発揮します。
斜光照明
斜光照明は浅い入射角で側面から光を当てることで、表面の微細な傷や埃が逆に明るく浮かび上がる現象を利用します(暗視野効果)。平滑な面では全体が暗く見える一方、傷の部分だけが光を散乱して光るため、通常見えにくい欠陥を検出できます。
同軸照明
同軸照明はビームスプリッタ(ハーフミラー)を用いてカメラと同軸上から光を照射する仕組みで、平滑な表面では反射光がそのままカメラに戻り均一な明るさの像が得られます。鏡のような面の細かな傷は正反射光では暗く写るため、同軸照明を使うと鏡面傷を黒い線として検出しやすくなります。
ドーム照明
ドーム照明は対象物を半球状の白いドーム内に置き、内側全面から拡散した光で包み込む手法です。影や反射のムラを極限まで無くせますが、装置が大型になりがちな点と、全方向から光が入るためコントラストが低下しやすい点に注意が必要です。
検査対象の形状や表面性状に応じて、これらの照明方法を使い分けることで欠陥検出の効率を高められます。
4. 照明配置の最適化と環境対策
いくら適切な照明を選定しても、その配置方法や周囲環境への配慮が不適切であれば、十分な検査精度は得られません。照明条件を最大限に活かすために、以下のようなポイントに注意して設置・調整を行います。
避けたい課題(問題点) | 有効な対策(改善策) |
---|---|
影の発生 | 拡散光を利用し、複数の光源で周囲から照らして影を埋める |
反射が強すぎて眩しい | 照明に偏光フィルターを装着、または同軸照明で正反射を避ける |
明るさが不均一 | 複数の照明を適切に配置し、照射エリア全体の均一化を図る |
環境光(外乱光)の影響 | 検査エリアを囲うカバーやケージを設置し外光を遮断する |
照明の不安定さ(光量変動) | 安定化電源を使用し、適切なウォームアップと定期校正を行う |
影の抑制
検査対象によっては一方向からの光だけでは死角が生じるため、ライトを複数配置して様々な方向から照射することが有効です。例えば上部と側面の両方から光を当てれば、一方でできた影をもう一方の光で打ち消せます。また拡散板を用いて光を柔らかくし、鋭い影をできにくくする工夫も影対策になります。
反射グレアへの対策
光沢表面では照明の映り込みで画像が白飛びすることがあります。偏光フィルターを照明側・カメラ側に使って反射光をカットすると効果的です。また同軸照明やドーム照明など反射を抑える手法を用いるのも有効です。
照度の均一化
画像全体で明るさが均等でないと、検査アルゴリズムが明るい部分ばかり検出したり暗い部分を見逃したりします。これを防ぐには、ライトの配置バランスを調整し、必要に応じて複数の照明を組み合わせて全体を均一に照らします。広いワークの場合はエリアごとに複数の同種照明を並べ、照度計などで各場所の明るさを測りながら均一に近づけるとよいでしょう。
環境光の遮断
検査専用の照明環境を維持するため、外界からの光をシャットアウトします。検査装置にカバーや遮光カーテンを設置して工場内照明や太陽光が検査エリアに入らないようにします。このように外乱光を遮断することで、時間帯や天候による明るさの変化に左右されず常に安定した条件で検査できます。
照明の安定化とメンテナンス
精密検査には、照明を事前に点灯して十分温めておく、安定化電源でフリッカを防ぐ等の対策が有効です。また定期的に光量を測定し、必要なら照明の交換・清掃を行うなど、メンテナンスも欠かせません。
5. 照明設定・調整の実践ステップ
最後に、実際に画像検査システムで照明を選定・調整する際の手順を、ステップごとに解説します。現場で最適な照明条件を見出すには試行錯誤が必要ですが、以下のようなプロセスで進めると効率的です。
ステップ1:検査対象の特性を分析する
検査対象の材質や表面状態(光沢や凹凸)と、検出すべき欠陥の種類をまず明確にします。例えば光沢金属表面の微細な傷を検出したい場合には、反射を抑えて傷を強調できる照明が必要です。このように目的と対象の性質を把握することが照明選定の出発点となります。
ステップ2:光源の種類と波長を仮決めして試行する
ステップ1を踏まえ、適切と思われる光源の種類と波長を選択し、サンプルを使って実際に照明を試します。複数候補がある場合は、色(赤・青・白)や光源(LED・ハロゲンなど)を変えて撮影し、欠陥が最も見えやすい条件を比較・評価します。
ステップ3:照射角度と距離を調整する
仮決めした照明で欠陥が写ったら、次に照射角度や距離を細かく調整します。光の入射角を浅くしたり深くしたり、照明と対象物の距離を変えることで、欠陥部分のコントラストが最大になる条件を探ります。必要に応じて別方向から補助の光を追加し、選んだ照明の効果を最大限に引き出します。
ステップ4:照明強度とカメラ露光を最適化する
照明の位置と角度が決まったら、照明の明るさとカメラの露光設定を最適化します。明るさが不足していれば光量を上げ、逆に白飛びする場合は光量を絞ります。同時にカメラの絞りやシャッター速度も調整し、欠陥部分が飽和しないようにします。高速ラインではストロボ照明をカメラと同期させるなど、鮮明で安定した検査画像が得られるよう工夫します。
ステップ5:環境条件の最適化と検証の繰り返し
設定が整ったら、実際の検査環境で結果を検証します。良品と不良品のサンプルで欠陥が確実に捉えられるか、誤検知が発生しないか確認しましょう。もし検出漏れや誤判定があれば、再度照明の種類・角度・強度を見直して微調整します。こうした検証と調整を繰り返すことで、現場環境で安定して動作する最適な照明設定が完成します。決定した条件は記録し、誰でも再現できるよう管理することも大切です。
まとめ
画像検査における照明の選定・設定は、検査精度を左右する極めて重要な工程です。
ポイントまとめ
✔ 検査対象に応じて最適な光源種類・波長を選定する(赤色光・青色光・赤外線・UVなど、対象物や欠陥に合わせて使い分け)
✔ 照明の角度や照射方法を工夫し、影や反射を抑えて欠陥を浮き立たせる(斜光照明やドーム照明の活用など)
✔ 検査エリアを囲うなど環境光の影響を排除し、常に安定した明るさを確保する
✔ サンプルで事前に照明条件を検証・微調整し、最適な設定を追求する
適切な照明を選び抜き最良の条件に調整することで、画像検査の精度と信頼性は飛躍的に向上します。照明技術を味方につけて、高精度な外観検査を実現しましょう!
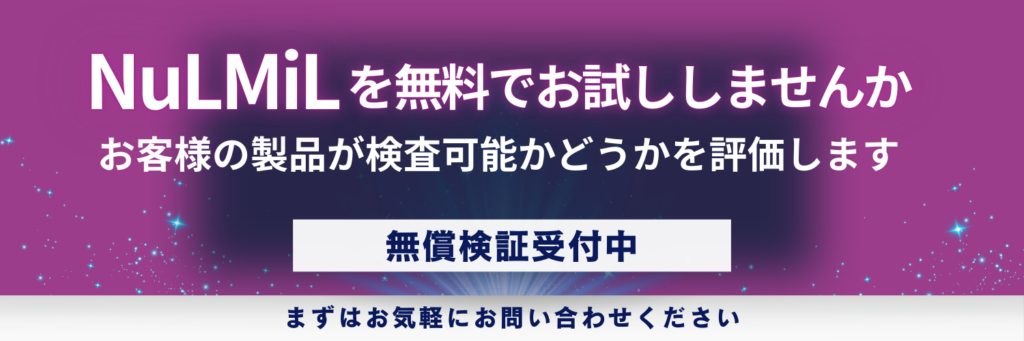