現代の製造業における品質検査では、製品の品質を確保するために様々な画像検査システムが活用されています。その中でも、ルールベース画像検査 と AI画像検査 は、品質保証の要となる二つの主要な方法です。それぞれの仕組みや特性、利点や課題を理解することで、検査対象に応じてどちらが最適かを判断できるようになります。本記事では、製造業の品質管理担当者向けに、AI技術の専門家の視点からこれら二つの画像検査手法の違いをわかりやすく解説し、適切な使い分けと今後の展望について考察します。
ルールベース画像検査とは
ルールベース画像検査の定義と概要
ルールベース画像検査とは、あらかじめ定めた基準やルールに従って画像データを解析し、製品の良否を判定する方式です。検査プログラム内に人間が設定したルール(例えば色のしきい値や寸法の許容範囲など)に基づき、不良の有無を自動判定します。コンピュータビジョン分野で古くから利用されてきた手法であり、明確な基準に沿った決定論的な検査が特徴です。
ルールベース画像検査に用いられる技術
ルールベース方式では、クラシックな画像処理技術を組み合わせて検査アルゴリズムを構築します。典型的な技術には、エッジ検出による形状の抽出、ヒストグラム分析による明暗や色の判別、テンプレートマッチングによるパターン照合などがあります。これらの手法を用いて画像中から欠陥や異常を定量的に判断できる特徴量を抽出し、事前設定したしきい値と比較することで合否判定を行います。
製造業におけるルールベース検査の適用事例
ルールベース画像検査は、製造業の様々な品質検査工程で古くから活用されてきました。特に判断基準が明確に定められる検査項目に適しており、例えばカメラで部品の寸法を測定して公差内か判定する寸法検査、必要な部品が全て取り付いているか確認する有無検査、表面に一定以上の傷がないかチェックする表面傷の検査などが典型的な適用例として挙げられます。こうした明確な基準の検査では、シンプルなルール設定によって安定した品質チェックが可能です。
ルールベース画像検査のメリット
ルールベース画像検査には、いくつかの優れた特性があります。第一に、判定基準があらかじめ決まっているため、一度システムを設定すれば安定した精度で高速な検査が可能です。画像処理の計算量も比較的軽いため、リアルタイムで大量の製品を処理するライン検査に向いています。第二に、AIのような大規模な学習データを必要としないため、検査アルゴリズムの構築が容易で初期導入コストを低く抑えられる利点があります。特に同じ仕様の製品を大量生産する現場では、シンプルなルールに基づいて効率的に品質チェックを行える点で有効です。
ルールベース画像検査の課題と限界
一方で、ルールベース検査には克服すべき課題も存在します。最大の課題は柔軟性の欠如です。ルールで明示できる基準以外の異常には対応できないため、製品バリエーションが多かったり、欠陥のパターンが複雑だったりする場合には検知漏れが発生しやすくなります。また、新しい不良モードが発生した場合や製品設計が変更された場合、その都度人手によるルールの追加・修正が必要です。メンテナンスの手間がかかり、検査システムの拡張性にも限界があると言えます。
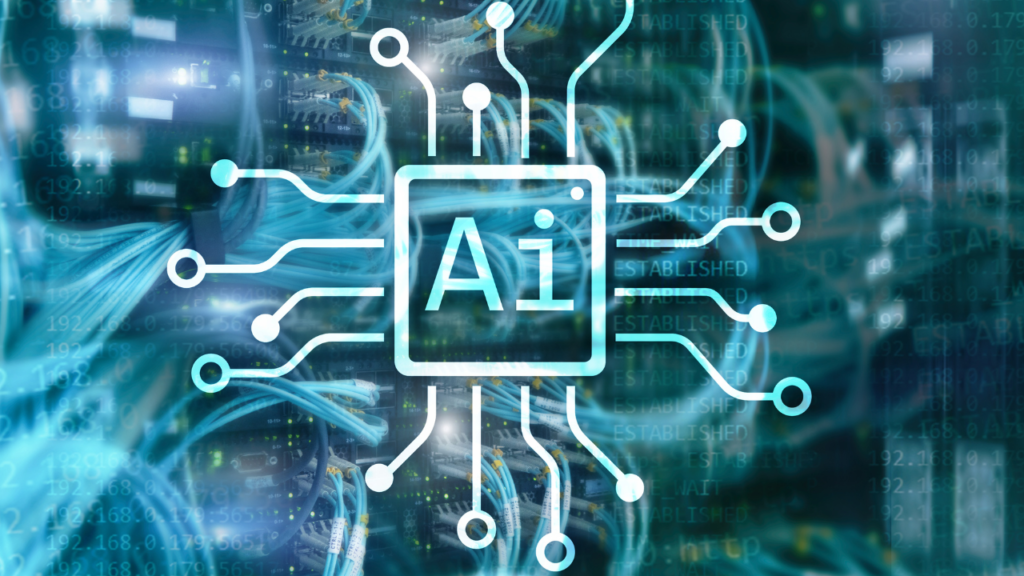
AI画像検査とは
AI画像検査の定義と概要
AI画像検査とは、ディープラーニングなどの人工知能(AI)技術を用いて画像内の不良を検出・分類する検査方式です。大量の製品画像データをAIモデルに学習させることで、良品と不良品の特徴を自動で学び取り、判定ルール自体をAIが形成します。従来のルールベースとは異なり、人が全ての判定基準をプログラムする必要がなく、AIがデータからパターンを習得していく点が特徴です。近年の深層学習技術の発展により、製造業の検査現場でも注目されるようになった新世代の画像検査アプローチです。
AI画像検査システムの仕組み
AI画像検査システムでは、まず開発段階で大量の画像データを用いてAIモデル(ニューラルネットワークなど)を訓練します。教師あり学習の場合、良品と不良品の画像をラベル付きで学習させ、不良品を識別する分類モデルを構築します。教師なし(良品のみ)学習の場合、良品データから正常パターンを学習し、それから逸脱する異常を検知する手法もあります。こうして作られたモデルを生産ライン上に組み込み、カメラから取得した画像に対して推論(インフェレンス)を行い、リアルタイムにOK品/NG品の判定を下します。AIが画像中の特徴を総合的に評価して判断するため、人が定義しきれない微妙な不良も検出可能です。
製造業におけるAI画像検査の適用例
AI画像検査は、従来のルールベース検査では検出が難しかった領域で活用が広がっています。形状が複雑な部品の欠陥検査、人の目では見落としがちな微細なキズ・異物の検出、良品のばらつきが大きい製品の検査などにおいて、AIが高い検出力を発揮します。こうした分野で、AI画像検査は従来手法では検知が難しかった外観検査の高度化に寄与しており、製造業の品質検査で新たな価値を生み出しています。
AI画像検査のメリット
AI画像検査には数多くのメリットが存在します。最大の利点は、複雑な外観上の特徴やパターンを捉える高い検出力と柔軟性です。人がルール化できないような曖昧な差異でも、AIが良品と不良品の違いを学習することで自動判別が可能になります。これにより、微細な傷・欠陥や多種多様な不良パターンにも対応でき、全体として検査の網羅性が向上します。さらに、AIモデルは学習データを追加することで継続的に精度向上を図れるため、運用を通じて検査能力を強化していける点も強みです。将来的な新種の欠陥に対しても、追加学習により比較的容易に適応できる拡張性を備えています。
AI画像検査の課題と注意点
一方で、AI画像検査を導入・運用する上では考慮すべき課題もあります。まず、モデルの構築には多数の画像データと時間が必要であり、不良品のサンプル収集やアノテーション(ラベル付け)には大きな労力を伴います。そのため初期導入コストが高くなりがちで、システム開発から現場適用までのリードタイムも長くなる傾向があります。また、AIの判断プロセスはブラックボックスになりやすく、「なぜ不良と判定したか」を人間が理解・説明するのが難しいという課題があります。さらに、高度なAIモデルをリアルタイムで動作させるにはGPUなど高性能なハードウェアが必要になる場合もあり、運用コストやインフラ整備にも留意が必要です。
ルールベース画像検査とAI画像検査の比較
検査精度・検出能力の比較
ルールベース検査は、条件が明確な場合には極めて高い精度で欠陥を検出できます。ただし、ルールで想定していない不良は見逃す恐れがあります。AI検査は多彩な不良パターンを識別でき、微細な欠陥にも対応可能です。一方で、AIの精度は学習データの質と量に左右され、不十分な学習では誤判定が起こる可能性もあります。
柔軟性・適応力の比較
ルールベース検査は設定された条件以外には適応できず、製品仕様の変更や新たな欠陥発生時に都度ルールの見直しが必要です。AI検査は学習データを追加することで新しいパターンにも対応でき、製品のばらつきにも柔軟に順応します。未知の欠陥でも、追加学習によって検出可能になるなど高い適応力を発揮します。
開発・導入コストの比較
ルールベース検査は事前の学習が不要でアルゴリズム開発も比較的容易なため、導入にかかる費用や時間を抑えやすいです。一方、AI検査は大量の画像データ収集とモデル学習が必要で、初期導入コストや期間が大きくなりがちです。また、高度なモデル構築には専門知識や高性能な計算環境も求められます。
運用・メンテナンス性の比較
ルールベース検査では、新たな欠陥や製品変更時にルールの改修が必要となり、エンジニアによる継続的なメンテナンスが欠かせません。AI検査では、運用中に精度を維持・向上させるため、追加のデータでモデルを再学習させてモデル更新を行います。再学習の工程は必要ですが、適切に運用すればモデルの継続的改善が可能です。
判定根拠の明確さの比較
ルールベース検査は判定基準が明示されているため、結果の理由を数値や条件で説明しやすいです。AI検査は内部の判断プロセスがブラックボックスになりやすく、なぜ不良と判定されたかを人が理解・説明するのが難しい場合があります。この説明性の違いから、AI検査を導入する際には判定根拠の可視化(説明可能なAI)も課題となります。
ルールベースとAI、それぞれの特徴をまとめると次の表のようになります。
比較項目 | ルールベース画像検査 | AI画像検査 |
---|---|---|
判定方法 | 人が定義したルールに従って判定 | 学習したモデルに基づき判定 |
判定根拠 | ホワイトボックス(理由が明確) | ブラックボックス(理由が不明瞭) |
必要なデータ量 | 少ない(基準設定のみ) | 多い(画像データ収集・学習が必要) |
主な利点 | 高速で安定、結果を説明しやすい | 複雑な欠陥も検出可能、変化に適応 |
主な課題 | 想定外の不良に対応困難、調整が必要 | データ準備の手間、結果の説明性に課題 |
ルールベース検査とAI検査の使い分け
基準が明確ならルールベース
検査基準を明確に定められる項目では、ルールベース方式がシンプルかつ確実です。寸法や有無のように閾値や許容範囲が設定しやすい検査では、人が定義したルールに従うシステムで十分な精度と安定性が得られます。
複雑な欠陥や変動にはAIが有効
傷の形状が多様、良品と不良品の差が微妙といった複雑な検査では、AI画像検査システムが威力を発揮します。人には基準を言語化しにくい検査対象でも、AIがパターンを学習することで高精度な自動検査が可能です。
データの有無に応じた選択
AI導入には多くの画像データが必要なため、不良品画像が十分に集まらない場合は効果を発揮しづらいです。データが集めにくい検査ではルールベース方式の方が適するでしょう。逆に豊富な画像データが蓄積できる現場では、AI検査を取り入れることでさらなる精度向上が期待できます。
人材スキルと既存システムの考慮
現場の技術リソースも考慮しましょう。AI画像検査を運用するにはAIやデータ分析の知識が必要となるケースがあります。自社に専門知識がない場合、従来から実績のあるルールベース手法の方が導入ハードルが低いと考えられます。一方、AIに詳しい人材がいる、または信頼できるAIシステム提供ベンダーと連携できる場合には、AI検査を導入することで品質管理の高度化を図りやすくなります。
ハイブリッド活用の検討
ルールベースとAIを組み合わせるハイブリッド運用も選択肢に入ります。例えば、まずルールベース検査で基礎的な項目を高速にチェックし、その後AI検査で微細な欠陥を検出する二段階方式により、双方の利点を活かすことができます。検査内容ごとに適した手法を使い分けることで、全体として品質検査の精度と効率を最大化できるでしょう。
進化する画像検査:ハイブリッド型の可能性
ハイブリッド型検査の概念
ハイブリッド型画像検査とは、ルールベース方式とAI方式の両方を組み合わせて検査を行うアプローチです。一つの検査工程内で両手法を補完的に用いることで、それぞれ単独では検出しきれない欠陥にも対応できる柔軟なシステムを構築します。
ハイブリッド型のメリット
ハイブリッド型の利点は、ルールベースとAIの強みを相乗的に活かせる点です。ルールベースの明確さとAIの柔軟性を両立させることで、検出漏れや誤判定を減らし、検査精度の向上が期待できます。特に単独の手法では判断が難しい境界ケースでも、二重の検査によって品質保証の信頼性を高められます。
ハイブリッド型の活用例
実際の製造ラインでハイブリッド手法を導入する例として、二段階検査のフローが考えられます。まず一次ステップでルールベース検査により寸法や有無など明確な基準項目を高速チェックし、続く二次ステップでAI検査により表面の微細な傷や予測困難な欠陥を検出します。このように工程を分けることで、生産ラインのスピードを維持しつつ広範囲の欠陥をカバーすることが可能です。
ハイブリッド型導入の課題
ハイブリッド手法の導入にあたっては、システムの複雑化に注意が必要です。二つの検査方式を統合すると装置構成や制御ロジックが複雑化し、導入や調整に余計な手間とコストがかかる恐れがあります。また、ルールベースの判定とAIの判定をどのように統合するか(例:片方がNGなら不良とする等)のルール設定も必要です。ハイブリッド化のメリットがコストに見合うかを見極め、必要性の高い場合に慎重に採用することが重要です。
ハイブリッド型検査の将来
将来的には、ルールベースとAIをよりシームレスに統合した検査システムが登場していくでしょう。AIモデルに人間が設定したルールを組み込む仕組みや、AIが自らルールを学習して調整する技術が進展すれば、ハイブリッド型の検査はますます洗練されると考えられます。ハイブリッド型は単に二つの手法を併用するだけでなく、互いの境界を融和させたスマートな品質検査システムへの道筋となるでしょう。
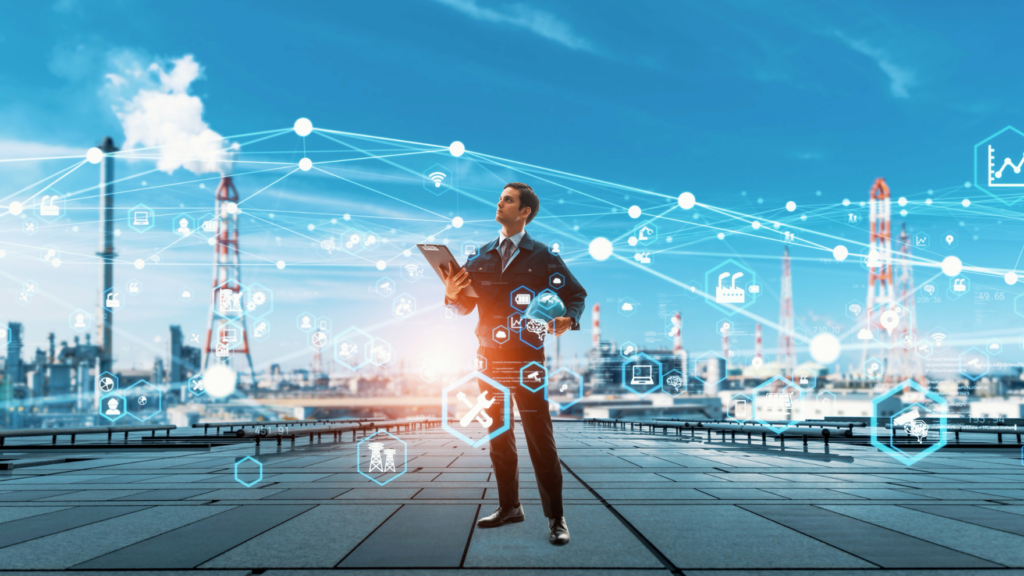
画像検査の未来展望
AI技術の進化と品質検査への影響
今後もAIおよび画像認識技術の進歩に伴い、画像検査の精度と効率は一段と向上していくでしょう。少量のデータでも学習可能な新たなアルゴリズムや、エッジデバイス上で高速動作する軽量なAIモデルが開発されれば、AI画像検査システムの導入ハードルはさらに下がると期待されます。これにより、従来は検出が難しかった欠陥も高精度に識別できるようになり、品質保証のレベルが全体的に底上げされるでしょう。
自動化と省人化のさらなる促進
製造業では人手不足や熟練検査員の減少が深刻化しており、検査工程の自動化・省人化ニーズは今後ますます高まります。AI画像検査の普及により、24時間稼働可能な自動検査ラインが実現し、人間による目視検査への依存を大幅に減らせます。これにより、作業者の負担軽減やヒューマンエラー防止につながり、安定した品質管理が可能となります。また、人員をより高度な付加価値業務に振り向けることで、生産性向上にも寄与します。
AI品質管理への発展
画像検査におけるAI活用は、品質管理全体のデジタル化・高度化、すなわちAI品質管理へと発展しつつあります。検査で得られた画像データや不良発生率をAIが分析し、不良の発生要因を予測して工程改善につなげるといった予防的品質管理も可能になってきました。単に不良品を排除するだけでなく、生産プロセス全体の品質を向上させるためにAIを活用する動きが広がっており、品質保証の在り方自体が変わり始めています。
人とAIの協調による品質保証
AIが高度化しても、人間の役割が不要になるわけではありません。今後は人間とAIがそれぞれの強みを活かして協調する品質保証体制が主流になるでしょう。例えば、AI画像検査の結果を人が最終確認する二重チェック体制が考えられます。人はAIでは難しい総合判断や改善策の立案に注力し、AIは繰り返しの検査作業や大量データの分析を担うことで、高度な品質保証を実現できます。
高度な画像検査システムへの道
ルールベース画像検査とAI画像検査は、品質検査システムの中核として今後も進化していくでしょう。現時点では両者を適材適所で使い分けることが重要ですが、将来的にはその境界が次第に融解し、AIの力を取り入れながら説明性と安定性を兼ね備えた高度な画像検査システムが実現するでしょう。製造業の品質管理担当者は、新たな検査技術の動向を注視し、自社に適した形で取り入れることで、品質管理のさらなる向上と競争力強化につなげることが重要です。
※2024/10/28公開 2025/4/25更新
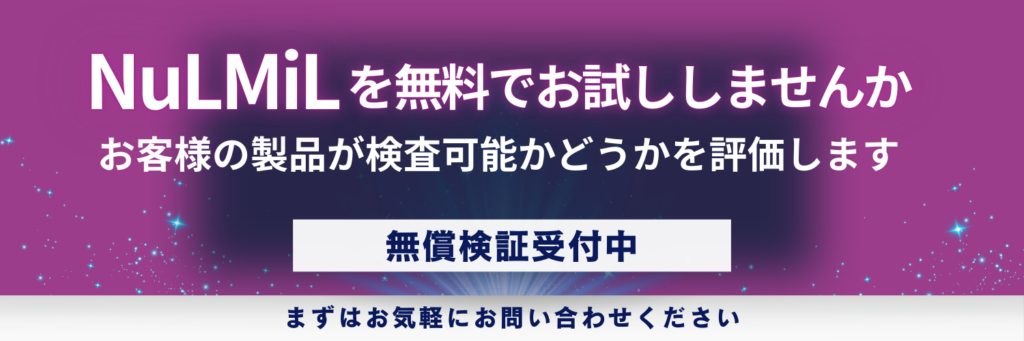